1. INTRODUCCIÓN
Es conocida la evolución del uso de los procesos de soldadura por arco eléctrico durante los últimos años [1]. En los países de Latinoamérica, esta tendencia ha sido menos marcada, empleándose hasta el 40 % del metal depositado en países como Argentina. En China y la India, acompañando el notable crecimiento de la producción de acero, se ha observado un marcado aumento del uso de electrodos revestidos. Todo parece indicar que el uso de electrodos revestidos se estabilizará en alrededor del 30 % del metal de soldadura depositado a nivel mundial [2].
El desgaste es parte de los procesos productivos, ya que los metales sufren los efectos de las partículas abrasivas que provocan pérdidas sensibles en los mismos.
La acción de estas partículas en el mecanismo de desgaste depende de múltiples factores, además de las características del material desgastado. La investigación sobre nuevos materiales para recargue es uno de los campos de mayores potencialidades para enfrentar fenómenos como el desgaste de piezas y componentes [3], [4].
El estudio adecuado de los mecanismos de desgaste contribuye en gran porcentaje a realizar la selección del consumible apropiado. En algunos casos, la pieza puede estar sometida a varios factores. No existe el consumible que resista todas las condiciones anteriores, pero, en la práctica, siempre puede encontrarse una solución para cada caso [5].
Varios son los criterios empleados para seleccionar un consumible a emplear en determinada aplicación. Nunca debe realizarse tomando como criterio un solo parámetro. Entre los parámetros empleados se encuentran los parámetros de fusión y deposición, los que permiten estimar la productividad del electrodo y poder compararla con la de otra conocida o ensayada bajo las mismas circunstancias.
Para ello, puede usarse la norma ISO 2401-72 [6], en la que se valoran como principales parámetros de consumo la eficiencia de deposición (RD) y el coeficiente de deposición (D) [7].
La evaluación de la estabilidad del proceso de soldadura empleando la digitalización de las señales experimentales de voltaje y corriente de soldadura [8]-[12]-[13] señala que sus espectros de frecuencia están determinados por la fenomenología del arco eléctrico, en función de las propiedades químico-físicas de las sustancias componentes del plasma y su inercia, entre otros aspectos, lo cual está de acuerdo a lo planteado por [14].
En la soldadura con corriente alterna (CA) suele suceder que las extinciones naturales del arco no siempre terminan con su reencendido en el siguiente semiperíodo del voltaje. Como resultado, la soldadura con CA es la más inestable de todos los procesos de soldadura, mientras la frecuencia de las extinciones de arco es, sin duda, el principal indicador objetivo de su ignición [9]. La estabilidad del arco en soldadura con corriente alterna se evalúa con base en la variación de la tasa media de incremento de la conductividad del espacio de arco (B+).
Para establecer criterios sobre la resistencia al desgaste a alta tensión se ha empleado el ensayo tipo abrasión con espiga para determinar los valores de este y el coeficiente de fricción de materiales durante deslizamiento [15], [16]. Este ensayo consiste en una prueba comparativa, comúnmente empleada para la evaluación del desgaste abrasivo en depósitos de soldadura [15], a través de la comparación entre la masa de metal perdida durante el ensayo [17].
Como objetivo del presente trabajo se plantea establecer una metodología para la selección de la mejor variante de electrodo a emplear ante el desgaste abrasivo a través de la identificación y uso de los principales parámetros que puedan arrojar criterio para ello.
No se han encontrado valoraciones sobre estos aspectos en electrodos con una estructura de doble revestimiento aplicados en el recargue, explícitamente en la literatura consultada.
2. METODOLOGÍA
2.1 Materiales
Para la obtención de los revestimientos en los electrodos estudiados, se precisó preparar dos cargas de materias primas, una para cada uno. Un revestimiento para garantizar los parámetros operativos del electrodo, constituido por un 70 % de la masa seca total, correspondiente a la composición comercial, reconocida internacionalmente como revestimiento rutílico E6012.
Otro revestimiento (30 % de la masa seca total) se diseñó para aportar la carga de aleación. Las proporciones de 70 y 30 % se asumen según recomendaciones de la literatura [18], y buscando asegurar que la estabilidad del arco no se comprometa con la variación de la posición de la carga de aleación en la estructura del revestimiento.
La carga de aleación está constituida por un 24 % de ferroaleaciones y un 6 % de grafito.
Se fabricaron tres tipos de electrodos con la misma composición química para el núcleo metálico y la carga de aleación ver Tabla 1. Igualmente, se empleó el mismo revestimiento ver Tabla 2, similar al de un electrodo E6012 [2]. El revestimiento de la carga de aleación para cada tipo de electrodo ocupó la misma área de la sección transversal del revestimiento, por tanto, la misma medida en el volumen y masa totales del revestimiento. El aglutinante empleado también fue común para todos los electrodos: silicato de sodio, con una densidad de 1,44 a 1,48 g/cm3, ocupando entre un 28 % y 30 % de la masa total del revestimiento.
Tabla 1 Composición química de las materias primas empleadas en la confección de los electrodos
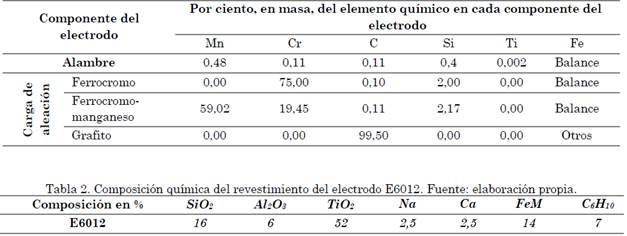
Fuente: elaboración propia
Las masas de revestimiento y carga de aleación involucradas en cada variante de electrodo se garantizaron iguales, a partir de la consideración del producto de la masa y la densidad de cada componente a través de sus respectivas áreas (A1 y A2), para cada caso (Fig. 1).
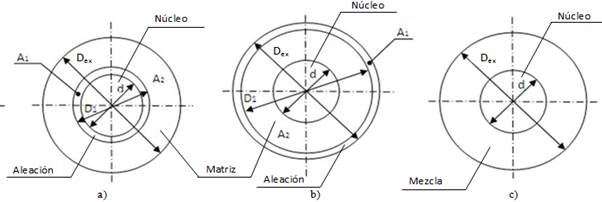
Fuente: elaboración propia.
Fig. 1 Esquemas geométricos de la conformación de los revestimientos en los electrodos a) doblemente revestido (la carga de aleación interna) b) doblemente revestido (la carga de aleación externa) c) simplemente revestido
Para la investigación, se estableció como estrategia comparativa la formulación de tres prototipos de electrodos, cuyas diferencias no estuvieran en su composición, sino en la posición que ocupan la carga de aleación y la matriz en la estructura del revestimiento del electrodo Fig. 1.
Como resultado se obtuvieron las dimensiones de los diferentes revestimientos para cada variante de electrodo desarrollado Tabla 3.
2.2 Métodos
La planificación experimental se estableció para satisfacer el objetivo del trabajo relativo a la evaluación del efecto de la posición que ocupa la carga de aleación (C-Cr-Mn) en la estructura del revestimiento de un electrodo para el recargue. Se tomó la posición de la carga de aleación en la estructura del revestimiento como factor independiente.
Por las características del experimento, fue conveniente el uso de un diseño completamente al azar (DCA) [19], [20].
El juego de hipótesis a contrastar al aplicar la prueba ANOVA a los datos, según el DCA, fue [19]:
H1: Algún par de medias de los tratamientos difieren (μi ≠ μj para algún i ≠ j; i= 1, 2, 3)
Como herramienta para procesar esta parte del estudio se empleó el software Statgraphics Centurion XV [21].
Ho: Las medias de los tratamientos son iguales (μ1 = μ2 = μ3)
Criterio de expertos
El método de criterio de expertos aplicado permite ordenar factores que emitan los expertos a partir del juicio.
Este método cuenta con los siguientes pasos: a) Selección del número de expertos; b) elaboración de la matriz de rangos con los criterios de los expertos a partir de la recolección de la información obtenida del juicio de cada experto; c) determinar el nivel de concordancia y realizar la validación del criterio de expertos [22].
El número óptimo de expertos se calculó en la expresión (1) a partir de la ecuación empleada por Duffus [23] en (1).
Donde, n es el número óptimo de expertos a seleccionar; i, nivel de precisión que se estima de 0,2; p, proporción del error que es de 0,10; k, para un 95 % de fiabilidad su valor es 3,84 y se identificó una población de expertos, N = 4.
Para procesar los datos recopilados se empleó el software profesional para procesamiento estadístico SPSS VS-23. Los criterios de estadística descriptiva se emplearon para conocer la evaluación del procedimiento respecto a cada uno de los principios que debe cumplir (el coeficiente de concordancia W de Kendall). Se calculó, además, el Índice de Validez de Contenido (IVC). Para estimar la fiabilidad del instrumento se empleó el estadígrafo alfa de Cronbach, el cual calcula la consistencia interna entre los parámetros que evalúan los expertos.
El criterio emitido por los expertos también se sometió al tratamiento estadístico anterior, y luego se obtuvieron las ecuaciones de regresión, que permiten obtener el peso de cada parámetro en estudio durante la definición de la mejor variante en el estudio de optimización.
3. RESULTADOS Y DISCUSIÓN
Se empleó un estudio de optimización por la complejidad de la valoración simultánea de todas las propiedades estudiadas y para identificar cuál de los electrodos podría tener un mejor desempeño.
3.1 Identificación de los factores independientes a considerar
Se identificó que los ensayos asociados al control del proceso de fabricación, como la resistencia mecánica y la excentricidad, satisfacen las normas empleadas, no aportando elementos de diferenciación entre las variantes de electrodos estudiados. Sin embargo, la higroscopicidad muestra diferencias, que pueden ser compensadas al aplicar los procedimientos estándares empleados durante la producción, conservación y uso de electrodos convencionales. En sentido general, si bien los ensayos valorados anteriormente sirven para evidenciar la calidad y reproducibilidad del comportamiento de los electrodos estudiados, los ensayos asociados al control de la calidad del proceso de fabricación no ofrecen parámetros robustos para ser considerados en una optimización.
Como parte de la evaluación del comportamiento operativo, se reconocieron como fundamentales los ensayos de estabilidad del arco y los relacionados con la determinación de los parámetros de consumo de los electrodos.
Se consideró la estabilidad del arco como uno de los indicadores operacionales principales del proceso de soldadura. Por otra parte, la estabilidad eléctrica del arco de soldadura constituye uno de los criterios de aceptabilidad o de calidad más reconocidos por los soldadores al emplear los electrodos. Además, existe el consenso de que un proceso de soldadura estable es el capaz de garantizar constancia en las dimensiones geométricas del cordón en toda su extensión [24]. Uno de los indicadores más robustos empleados para evaluar la estabilidad del arco en corriente alterna lo constituye la variación de la tasa media de incremento de la conductividad del espacio de arco (B+), que contiene variables energéticas esenciales del proceso. Además, ha sido validado y aplicado en múltiples estudios [25].
Por otra parte, la norma para la determinación de los parámetros de fusión y deposición [6] refiere en su alcance su suficiencia de uso práctico para medir con precisión las variaciones en el comportamiento de cada electrodo individualmente en cuanto a eficiencia, recuperación de material y coeficiente de deposición. Este último parámetro representa la masa de metal depositado por amperes y minutos de un electrodo dado, bajo las condiciones establecidas.
Este indicador no depende de otros parámetros geométricos del electrodo (largo total, longitud de colilla, etc.), lo cual lo hace más robusto para la comparación del comportamiento entre electrodos.
Para la evaluación de la calidad del metal depositado se realizaron ensayos para la determinación de la composición química, la caracterización microestructural, la medición de la dureza y la resistencia al desgaste. Dentro de ellos, la resistencia al desgaste en los depósitos constituye un ensayo definitivo de calidad del depósito de un electrodo destinado a disminuir el desgaste abrasivo [26]. Para la evaluación de la resistencia al desgaste se toman los datos resultantes del ensayo de “abrasión con espiga”, siendo el parámetro seleccionado la pérdida de masa, la cual resulta de la diferencia obtenida por medición gravimétrica de la masa inicial y final de la espiga ensayada, tomada durante un tiempo de 10 min.
La norma [27] considera como válido para la comparación de los resultados para ensayos realizados con el mismo tipo y grado de abrasivo.
Se consideran valores óptimos al evaluar el coeficiente de deposición 11,00·10-3 y 14,00·10-3 kg·(A·h)-1 y en el caso de la conductividad del arco (B+) valores por encima de 110 (Ω·s)-1 [27]. En el caso de la pérdida de masa, depende de las condiciones específicas del ensayo.
3.2 Aplicación del criterio de expertos
El número de expertos necesario en la expresión (1) fue de 3,04, por lo que se asumió una cantidad de expertos de tres.
Para seleccionar los integrantes más idóneos de la población considerada, se aplicó una encuesta estructurada para determinar el nivel de competencia de cada experto. Seguidamente se sometió a criterio de los expertos el procedimiento a emplear, para evaluar si posee validez de contenido (IVC); es decir, que posee carácter sistémico, consistencia lógica, equilibrio entre cada fase, flexibilidad y pertinencia [23]. El índice de validez de contenido (IVC) que se obtuvo es de 0,83; este valor es suficiente para valorar positivo el criterio del grupo respecto al ítem de evaluación.
El nivel de concordancia de los jueces (W Kendall) que se obtuvo es de 0,667 y la fiabilidad por el estadígrafo de alfa de Cronbach es 0,831, lo cual ratifica la herramienta como fiable.
3.3 Resultados de la aplicación del criterio de expertos a la selección de la mejor variante
A los expertos se les entregó una encuesta con los resultados aleatorizados de todos los experimentos y sus respectivas réplicas, cuyos resultados se conjugaron posteriormente con la codificación inicial en Tabla 4.
Atendiendo al ordenamiento realizado por los expertos (Tabla 4), según los criterios anteriormente establecidos, se pueden conformar tres grupos de resultados: grupo A, con los números de las corridas 7, 3 y 6; grupo B, con los números de las corridas 8, 5 y 2; y grupo C, con los números de las corridas 9, 4 y 1. Cada grupo puede asociarse con la denominación externa, homogénea e interna, respectivamente (Tabla 4).
Los expertos reconocen las características producidas por la aplicación de la carga de aleación en la parte externa del electrodo como las de mejor desempeño, continuando en su ordenamiento, de forma descendente, con los electrodos que poseen la carga distribuida homogéneamente, y, por último, los que contiene la carga de aleación ubicada internamente.
Se obtuvo un nivel de concordancia de los jueces (W Kendall) para los juicios emitidos de 0,941, y la fiabilidad por el estadígrafo de alfa de Cronbach es 0,969, lo cual reconoce a la herramienta como muy fiable.
El ordenamiento realizado por los expertos se procesó para obtener ecuaciones de regresión en Tabla 5 que permiten explicar matemáticamente el peso de las consideraciones asignadas por los expertos a cada factor estimado sobre el conjunto de resultados evaluados.
De la Tabla 5 se puede apreciar en la pérdida de masa que el factor X2 es el que mayor significación obtuvo en la evaluación de los expertos, siguiendo en orden descendente el coeficiente de deposición (X1) y la conductividad del arco (X3).
Tabla 5 Ecuación de regresión obtenida según el criterio de evaluación de cada experto

Fuente: elaboración propia.
Este resultado muestra, tanto en la evaluación individual (Ecuaciones de la 2 a la 4) como en la integrada (Ecuación 5), la importancia que los expertos le confieren al factor dependiente “resistencia al desgaste”, contraria a la que le dan a la estabilidad del arco. Esto se debe a que el valor de B+ está dentro del rango de una conductividad eléctrica aceptable en las tres variantes.
El análisis (Tabla 5) muestra que la variante con mejores prestaciones para el proceso de recargue es la que posee la carga de aleación ubicada externamente en la estructura del revestimiento de los electrodos evaluados. Además, esta variante constituye un nuevo prototipo de electrodo doblemente revestido, caracterizado por presentar un revestimiento interno ordinario, empleada para electrodos de soldadura (E6012), y otra externa, compuesta por una carga de aleación (C-Cr-Mn), cuya aplicación es la aportación de recargues resistentes al desgaste abrasivo.
4. CONCLUSIONES
Los expertos reconocen que los parámetros más representativos para someter al criterio de los expertos son los resultados de la variación de la tasa media de incremento de la conductividad del espacio de arco (la estabilidad del arco), del coeficiente de deposición (parámetros de fusión y deposición) y del ensayo de abrasión con espiga (resistencia al desgaste).
Se selecciona unánimemente como la mejor variante de electrodo doblemente recubierto la que posee la carga de aleación externa, seguida de la variante con carga de aleación homogéneamente distribuida y, por último, la que posee la carga de aleación interna, a partir de una relevancia asignada a las variables de pérdida de masa (224), coeficiente de deposición (77) y estabilidad del arco (0,01).
Los resultados del análisis realizado para la selección de la mejor variante sugieren que la resistencia al desgaste, evaluada a través de la pérdida de masa, es el criterio de mayor relevancia a considerar en la metodología para la selección de electrodos destinados al recargue de piezas.