1. INTRODUCCIÓN
El titanio es un material metálico que tiene excelentes propiedades mecánicas como su buena resistencia a la corrosión, resistencia a altas temperaturas y biocompatibilidad [1]. Este metal es utilizado en la industria aeroespacial donde se encuentra presente en componentes de aeronaves como turbinas de gas, en las cuales, aproximadamente la tercera parte de sus componentes están fabricados de titanio; por ejemplo, los alabes de los compresores fueron el primer componente fabricado en este material. También es utilizado por fabricantes de automóviles como Volkswagen que lo implementó en la construcción de muelles para la suspensión y algunos componentes de los motores como válvulas; otra de sus aplicaciones y una de las más importantes, es la fabricación de prótesis óseas debido a que este material presenta buena biocompatibilidad con el cuerpo humano [2]. El titanio es un material utilizado en muchos campos de la industria, como en la aeroespacial, naval, automotriz y biomédica [3].
La alta resistencia específica del titanio junto con la estabilidad metalúrgica a altas temperaturas y las bajas tasas de fluencia, hacen que sea favorable para componentes de motores a reacción como alabes y discos en las secciones bajas e intermedias de los compresores [4]. Productos de titanio como muelles también se utilizan en los autos de carreras y motocicletas. La aplicación más reciente de titanio está en la arquitectura, un concepto utilizado por primera vez en Japón [5].
En la industria aeroespacial se utiliza en la construcción de las turbinas a gas. En la naval debido a su alta resistencia a la corrosión, se utiliza en la construcción de hélices, ejes de timón y en cualquier parte que se encuentre en contacto con el agua salada. De igual manera, en la industria biomédica, se utiliza principalmente para la construcción de prótesis de articulaciones (codo, rodilla, cadera, etc.) debido a su compatibilidad con el tejido humano, al no generarse rechazo del sistema inmunológico hacia el material [3].
Aunque el titanio es un material muy utilizado y apetecido en muchos campos de la industria, tiene un gran problema y es su baja resistencia al desgaste, lo que genera que su vida útil sea menor comparada con otros materiales; además la película de óxido producida naturalmente presenta una resistencia mecánica baja, disminuyendo algunos de sus aplicaciones.
Por lo anterior se han venido desarrollando diferentes tipos de tratamientos superficiales para mejorar las propiedades mecánicas y tribológicas del titanio y sus aleaciones [6], [7]. La oxidación térmica es un tratamiento de modificación superficial utilizado para mejorar la resistencia al desgaste del titanio; este consiste en aumentar el espesor de la capa de óxido que se forma naturalmente en la superficie del titanio, formándose una serie de estructuras cristalinas y amorfas que mejoran las características del material; entre ellas encontramos los principales óxidos de titanio como la anatasa, el rutilo y la broquita.
La fase rutilo es más densa que la anatasa, 4,240 g/cm3 y 3,830 g/cm3 respectivamente, lo que como consecuencia causa que las estructuras presenten propiedades distintas. La estructura anatasa podría transformarse rutilo a altas temperaturas debido al rompimiento de los enlaces de TiO2 permitiendo un reacomodo del octaedro, generando una disminución en el volumen y la aparición de dicha fase. El rutilo es la fase más estable a distintas temperaturas debido a que presenta menor energía libre de formación. Sin embargo, la transformación de fase también se puede presentar por imperfecciones en la red cristalina como la debilidad de algunos enlaces, impurezas y variación de la atmósfera exterior [8], [9].
Este tratamiento de modificación superficial le da al titanio una mayor resistencia al desgaste a la que posee el material naturalmente, y con un menor costo en comparación con otros procedimientos como el anodizado, o recubrimiento PVD (Chemical Vapor Deposition) entre otros [10], [11]-[13].
Bloyce y col. (14), realizaron un estudio en aleaciones de titanio para mejorar conjuntamente la corrosión y el desgaste, en este estudio fueron aplicados tres tratamientos, nitruración con plasma, oxidación térmica tratada con paladio y oxidación térmica. La oxidación térmica se llevó a cabo a 600ºC y 900°C con 2 y 4 horas respectivamente de sostenimiento, encontrándose especialmente rutilo, con un mejor comportamiento respecto a la corrosión; por otra parte, en un estudio desarrollado por Güleryüz y col. [15], estudiaron el efecto de la oxidación térmica en la corrosión y el comportamiento al desgaste por corrosión, se desarrollaron pruebas a 600ºC y 650ºC con tiempos de 12 y 60 horas. En las pruebas sometidas a 600ºC se encontraron estructuras α, anatasa y rutilo, mientras que en las muestras sometidas a 650ºC solo se encontró rutilo. La dureza superficial de ambos tratamientos mostró un incremento al aumentar la temperatura y el tiempo del proceso, y la resistencia a la corrosión máxima se obtuvo a 600ºC y 60 horas [15]. Para el caso de la resistencia a la corrosión Kumar y col. [16], analizaron esta característica como una función del tiempo de tratamiento de oxidación térmica en el cual se sometieron las muestras a una temperatura de 650ºC, con tiempos de 8, 16, 24 y 48 horas, allí se encontró un aumento de dureza, rugosidad, espesor de la película y resistencia a la corrosión, en función del tiempo de tratamiento, de igual forma, Satendra y col. [13], encontraron resultados muy similares por efecto del tiempo y temperatura de tratamiento; sin embargo, el efecto de la velocidad de enfriamiento fue evidenciado por Jamesh y col. [7], quienes trabajaron con temperaturas de tratamiento de 650°C y 850°C y tiempo de 8 y 14 horas pero con velocidades de enfriamiento de 5°C/min, en este caso el espesor de película aumentó, se encontró rutilo como estructura cristalina, sin embargo, velocidades de enfriamiento rápidos disminuye la resistencia a la corrosión[17].
En esta investigación se analizó el efecto de la oxidación térmica en la obtención de estructuras cristalinas y su efecto en propiedades de dureza y cambio microestructural en la aleación Ti6Al4V.
2. METODOLOGÍA
2.1 Material base
Se seleccionó la aleación Ti6Al4V, el material fue suministrado en barra circular de un metro de longitud y 14 mm de diámetro. La tabla 1 muestra la composición general de la aleación Ti6Al4V según la norma ASTM F-136.
Tabla 1 Composición de la aleación de titanio Ti6Al4V según norma ASTM F-136 (18).
COPMPOSICIÓN (wt%) | ||||||||
---|---|---|---|---|---|---|---|---|
Elemento | Al | V | Fe | C | O | N | H | Ti |
% peso | 5,5-6,5 | 3,5-4,5 | 0,25 | 0,08 | 0,13 | 0,05 | 0,012 | Bal |
De una barra de titanio Ti6Al4V se realizaron cortes transversales de 5 mm de espesor cada uno, por medio de electroerosionadora por hilo a baja velocidad y refrigerada, para disminuir al máximo el calentamiento de las piezas. Las muestras utilizadas para el análisis metalográfico y el posterior tratamiento de oxidación térmica fueron sometidas a un proceso de desbaste y pulido, establecido por la norma ASTM E3-01. Para el análisis metalográfico fue realizado un ataque químico durante 30 segundos con reactivo Kroll (100 mL H2O + 6 mL HNO3 + 3mL HF) para revelar la microestructura.
2.2 Oxidación térmica
El tratamiento de oxidación térmica se llevó a cabo en un horno de resistencias con controlador automático (marca Terrígeno, serie 503). Las muestras fueron sometidas a temperaturas entre 450°C y 850ºC, con intervalos de 100°C a una velocidad de calentamiento de 4ºC/min, y un tiempo de sostenimiento de 2 horas, y enfriamiento lento dentro del horno. Las muestras sin tratamiento son designadas como Ti64-ST, y las muestras oxidadas térmicamente se designa como OT-450, OT-550, OT-650, OT-750, y OT-850 según sea la temperatura de tratamiento.
2.3 Caracterización microestructural
La caracterización microestructural del material base sin tratamiento se realizó mediante un microscopio metalográfico marca Olympus GX51. Para las muestras oxidadas térmicamente se caracterizaron mediante microscopía electrónica de barrido en un microscopio marca JEOL 5910LV. Por medio de espectroscopía de dispersión de energía de rayos X (EDS) se obtuvo la composición química de las muestras, realizándose tres medidas en puntos diferentes de la muestra, y determinando una relación titanio-oxígeno.
Para conocer las diferentes estructuras cristalinas de los óxidos obtenidos en cada uno de los procesos de oxidación térmica, fue utilizada difracción de rayos X en un equipo marca PANalytical XPert Pro MPD, la radiación usada fue de tipo Kα del Cu (L=1,5418 Å) operando a 45 kV y 40 mA. Además, se realizó un ensayo de difracción de rayos X sobre una muestra en la cual se llevó a cabo un proceso continuo de calentamiento isotérmico desde temperatura ambiente hasta los 900°C.
Para determinar la dureza de las muestras fue utilizado un microdurómetro marca Akashi modelo MVH-O, el ensayo se llevó a cabo con una carga de 200 g y un tiempo de 15 s, con tres ensayos por muestra.
3. RESULTADOS Y DISCUSIÓN
3.1 Material base
La figura 1 muestra la sección longitudinal (a) y la sección transversal (b) de la aleación de titanio Ti6Al4V sin tratamiento térmico. En la figura 1 se puede apreciar que la aleación Ti6Al4V posee una matriz β contenida en α, donde las partes oscuras pertenecen a la estructura β y las partes claras corresponden a la estructura α. En la figura 1a se pueden observar unos granos con forma alargada, debido a la deformación a la que se ve sometida el material en su proceso de fabricación, mientras que en la figura 1b se ve una forma de grano más equiaxial y uniforme en toda la estructura.
3.2 Oxidación térmica
La tabla 2 muestra la composición química de cada una de las muestras oxidadas térmicamente desde 450ºC a 850ºC. Esta composición fue tomada por medio de la técnica EDS (espectroscopía de dispersión de energía de rayos X) y nos permite hacer un análisis cualitativo de la composición química de las muestras.
Tabla 2 Composición química de las muestras de Ti6Al4V oxidadas térmicamente desde 450ºC a 850ºC.
MUESTRA | COMPOSICION (At. %) | |||||
---|---|---|---|---|---|---|
Ti | Al | V | N | O | Relación O/Ti | |
OT-450 | 86,96 | 9,87 | 3,17 | N/A | N/A | No Aplica |
OT-550 | 55,01 | 5,46 | 2,05 | 4,07 | 33,41 | 0,6 |
OT-650 | 37,91 | 5,86 | 1,82 | N/A | 54,41 | 1,43 |
OT-750 | 28,92 | 8 | 0,89 | N/A | 62,19 | 2,15 |
0T-850 | 36,75 | 20,1 | 2,01 | N/A | 41,14 | 1,11 |
En la figura 2 se pueden observar las micrografías de la vista transversal de las superficies de estudio que fueron sometidas a oxidación térmica entre 450ºC y 850ºC, con un tiempo de mantenimiento de dos horas. La figura 2a y 2b no presentan un crecimiento significativo de cristales. Para las muestras OT-650 (fig. 2c), OT-750 (fig. 2d) y OT-850 (fig. 2e) es apreciable la aparición de formas cristalinas que se van incrementando con la temperatura formándose una película de óxido (con el incremento de temperatura hay una mayor difusión de oxígeno) según se muestra por la relación oxigeno/titanio que va incrementándose como se muestra en la tabla 2.
Por otra parte, las muestras oxidadas a 850°C presentaron una disminución de esta relación O/Ti, esto debido a que a temperaturas superiores a 700°C es termodinámicamente más favorable la formación de óxidos de aluminio (Al2O3), lo que causa la disminución del porcentaje de oxígeno disuelto en la aleación [19], [20].
A partir de 650°C se observa la presencia de cristales uniformes en la superficie de la muestra, estos a su vez van aumentado su tamaño a medida que se aumenta la temperatura de oxidación.
Al llegar a 750°C el crecimiento es aleatorio con respecto a su posición en forma de picos perpendiculares a la superficie de la muestra. Con el aumento de temperatura hasta llegar a 850ºC la forma de los cristales de óxido empiezan a cambiar, siendo muy similares entre sí, más finos y de forma alargada cubriendo la superficie de la muestra de manera más uniforme.
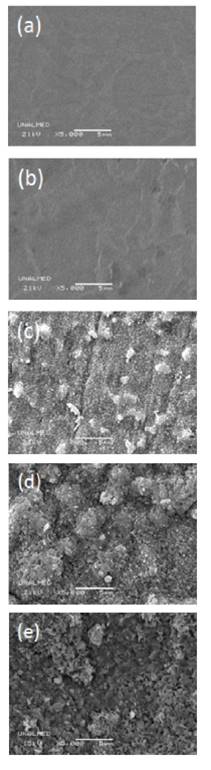
Figura 2 Micrografía de las muestras de titanio oxidadas térmicamente (a) OT-450, (b) OT-550, (c) OT-650, (d) OT-750 y (e) OT-850.
En consecuencia, la nucleación de óxido se lleva a cabo a lo largo de la superficie cuando se entra en contacto inmediatamente con el oxígeno, mientras que el modo de crecimiento implica la formación de una cascarilla de óxido delgada seguido por su aglomeración y el crecimiento, para cubrir completamente la superficie [13].
3.3 Espesor de película
La figura 3 muestra la vista de la sección transversal de la película de óxido formada en las muestras que fueron sometidas a oxidación térmica a 650ºC, 750ºC y 850ºC; en ellas se encontraron espesores de 2,03±0,28µ, 5,88±0,68µ y 14,64±0,78µ para 650°C, 750°C y 850°C respectivamente, mientras que Jamesh y col. (7), encontraron que para las mismas condiciones a 650°C pero con tiempos de 14 horas, sólo se alcanzaron espesores aproximados de 1µ.
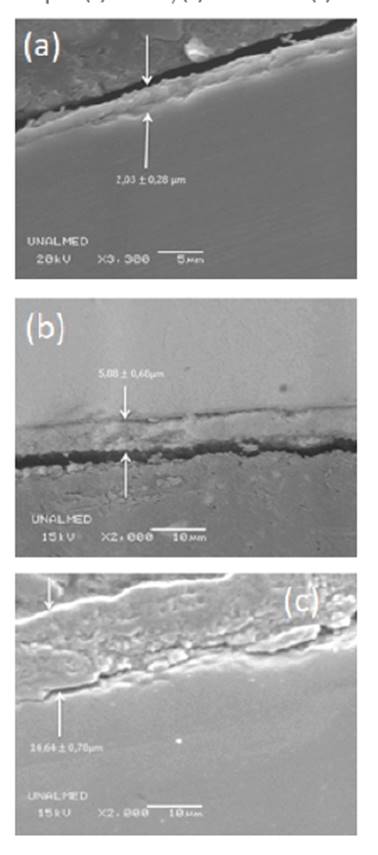
Figura 3 Vista de la sección transversal de las películas de óxido obtenidas en las muestras (a) OT650, (b) OT-750 y (c) OT-850.
A partir de la temperatura de 850°C se observa que la capa de óxido formada en la superficie se empieza a desprender, esto debido a la diferencia de coeficientes de dilatación térmica entre el material base (Ti6Al4V) y el óxido formado en la superficie [21], sin embargo, en el estudio desarrollado por Jamesh y col., se encontró que tiempos prolongados de enfriamiento favorecen la adhesión de la película a esa temperatura de tratamiento.
3.4 Ensayo de microdureza
La figura 4 muestra los valores de dureza y espesor de película de óxido para las diferentes muestras tratadas térmicamente. Con el incremento de temperatura, además de la formación de la película de óxido, también se presentó un incremento de la dureza especialmente con temperaturas mayores a 550°C, con un incremento a los 850°C (782HV0.2) del 41% con respecto al material base (Ti6Al4V = 324 HV0.2), como se evidenció en [22].
Kumar y col., encontraron en su estudio incremento de dureza pero con un incremento del tiempo de mantenimiento para temperaturas de 650°C, mientras que la presente investigación presentó incremento de dureza de 410 HV0.2 comparado con Kumar y col., que fue de 365 HV0.2 y 395 HV0.2 para 8 y 16 horas respectivamente [19].
En las muestras OT-450 y OT-550 se presentó un cambio pequeño de dureza (327 HV y 382 HV respectivamente), con respecto a la aleación sin tratar (Ti6Al4V = 324 HV0.2).
3.5 Difracción de rayos X
La figura 5 muestra los difractogramas de rayos X de cada una de las muestras oxidadas térmicamente con variación de temperatura entre los 450°C y 850°C. En la curva de la muestra de Ti6Al4V sin tratamiento se aprecia la aparición de picos de titanio α y titanio β en la estructura, los cuales se mantienen en las curvas de 450°C y 550°C debido a que no hubo transformaciones de fase en la estructura. A partir de 650°C se muestran transformaciones de fase y aparece un pico de anatasa en el ángulo 25°,335’, (en la figura 6 se puede observar claramente la existencia de este pico en el difractograma a partir de los 650°C) que posteriormente desaparecerá en las siguientes temperaturas; hacia los 650°C empiezan a aparecer picos de rutilo de baja intensidad en 27⁰,436’, 36⁰,080, 54⁰,321’ y 62⁰,759’; que seguirán aumentando su intensidad a 750°C y 850°C en donde sólo se observan picos de rutilo.
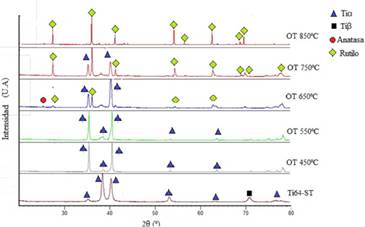
Figura 5 Difractograma de rayos X de muestras de Ti6Al4V oxidadas térmicamente con variación de temperatura entre 450ºC y 850ºC.
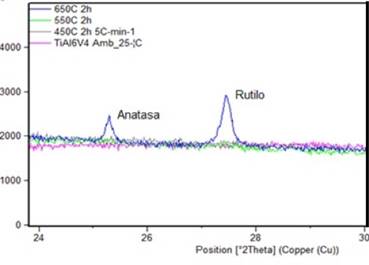
Figura 6 Difractogramas de rayos X para las muestras oxidadas térmicamente entre los ángulos 24° y 30°.
La figura 7 muestra el difractograma de rayos X de la muestra de Ti6Al4V para un proceso continuo de calentamiento isotérmico desde temperatura ambiente hasta los 900ºC. En la muestra de aleación Ti6Al4V sin tratamiento térmico se encontraron principalmente dos fases en la estructura, en los picos a 35⁰, 38⁰, 40⁰, 53⁰, 63⁰ y 78⁰, 1’ se encontró titanio α y en el pico a 71° se encontró titanio β. A 450°C no hubo ninguna transformación de fase con respecto al titanio sin tratar, por lo tanto, se mantuvieron las mismas estructuras de titanio α y titanio β en los mismos ángulos, aunque con un aumento en la intensidad de los picos de difracción, tal vez debido más a un fenómeno de textura cristalográfica que a otro aspecto.
A partir de la temperatura de 550°C se empiezan a observar las primeras transformaciones de fase ya que la estructura titanio α empieza a cambiar y aparece el primer pico de anatasa en el ángulo 37⁰,809’ y en el ángulo 39⁰,223’ aparece un pico de TiO2, que posteriormente desaparecerá hacia la temperatura de 650ºC, sin embargo, el pico de anatasa a 37⁰,809’ aumentará su intensidad hasta los 750°C y hacia los 850°C se transformará en rutilo. Los primeros picos de rutilo empiezan a aparecer por encima de los 650°C, es así como a los 750°C, se observan cinco picos correspondientes a esta fase en los ángulos 27⁰,46’, 36⁰,08’, 54⁰,321’, 62⁰,759’ y 69⁰,802’ que con el aumento de temperatura aumentan su intensidad; ya a los 850ºC, sólo se muestran estructuras de rutilo en toda la superficie.
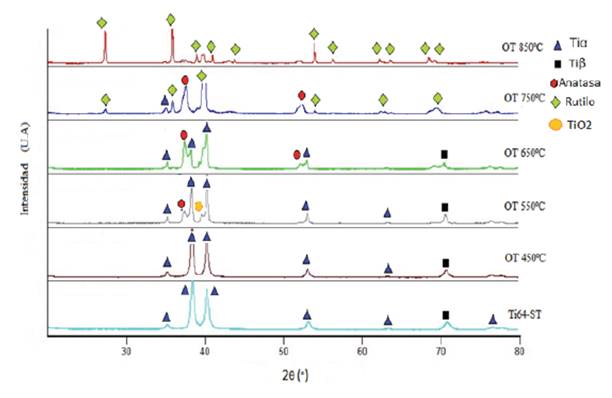
Figura 7 Difractograma de rayos X de la muestra de Ti6Al4V para un proceso continuo de calentamiento isotérmico desde temperatura ambiente hasta los 900ºC.
Para los dos difractogramas (figuras 5 y 7), se puede observar que, desde temperatura ambiente hasta 550°C, se encontraron las mismas estructuras correspondientes a titanio α y titanio β. Sin embargo, en la figura 7 además de estas estructuras bases también se encontró un pico de anatasa y un pico de TiO2, caso contario a la figura 5 donde los primeros picos de anatasa empiezan a aparecer desde la temperatura de 650°C, lo anterior posiblemente al proceso continuo de calentamiento que favorece las transformaciones de fase por la estabilidad del tratamiento. El proceso continuo isotérmico mostró que a partir de 800°C ya se muestra en totalidad estructuras de rutilo en su superficie.
Por otra parte Güleryüz y col. [15], encontraron que a temperaturas y tiempos de mantenimiento altos, la totalidad de la fase que se puede encontrar es rutilo, sin embargo a temperaturas menores a 650ºC es posible encontrar fases correspondientes a anatasa, como es observable en la figura 7 donde se encontraron picos de anatasa a temperatruas por debajo de los 650°C. Sin embargo, estos picos de anatasa se transformaron y a temperaturas superiores a 650°C sólo se observan mayormente picos de rutilo.
4. CONCLUSIONES
Con el incremento de temperatura, las muestras de la aleación Ti6Al4V, que fueron sometidas a procesos de oxidación térmica, mostraron la formación de una película de oxido tipo TiO2, la cual incrementó su espesor con el aumento de temperatura. Se encontraron espesores desde 2,03 ± 0,28µm para la probeta oxidada a 650°C hasta 14,64 ± 0,78µm para la probeta oxidada a 850°C, en tiempos de tratamiento de 2 horas.
Se observó una variación significativa de dureza en muestras oxidadas termicamente con relación a muestras sin tratamiento. Con el incremento de temperatura se presentó un incremento de dureza, alcanzándose valores de 781,2 HV 0,2 para las muestras oxidadas a 850°C, es decir un incremento de 40% en relación a la dureza del material base que fue de 324,2 HV0,2.
Los ensayos de difracción de rayos X, mostraron la presencia de estructuras tipo TiO2 y Ti2O3, principalmente estructuras de anatasa y rutilo. A partir de 650°C empiezan a evidenciarse los primeros picos de rutilo y anatasa; sin embargo, después de los 800°C la fase predominante es el rutilo.
La muestra oxidada a 850°C presentó desprendimiento de la capa de óxido debido a la diferencia entre coeficientes de expansión térmica entre el substrato y la capa de óxido, lo que genera esfuerzos de compresión en el momento del enfriamiento.