Introducción
En la actualidad, las empresas se enfrentan a una competencia sin fronteras, donde existe la necesidad urgente de cambiar la forma tradicional de operar las compañías, optimizar los procesos y reducir los desperdicios de tiempo, costo y espacio que se generan dentro de los mismos (Barcia & De Loor, 2007). Por este motivo, muchas organizaciones están buscando identificar la cadena de valor en cada uno de sus procesos. Se debe tener en cuenta que la cadena de valor se define como aquellas actividades que le dan un valor agregado al cliente y que involucra todo el camino que debe seguir el producto desde la recepción del pedido hasta la entrega al cliente final (Nash & Poling, 2008). En el presente estúdio se pretende optimizar el proceso de recepción, unificación, almacenamiento y alistamiento de corrugado de una empresa nacional que se dedica al empaque de todo tipo de cristalería como platos, vasos, ensaladeras, licoreras, copas, etc.
Para la determinación de los problemas asociados al proceso, se utilizará la herramienta conocida como Value Stream Mapping (VSM) o mapeo de la cadena de valor, debido a que autores como Nash y Poling (2008) han logrado concluir que esta técnica permite, a los stakeholders1 de una organización, visualizar y entender el proceso; además permite reconocer el valor, diferenciarlo del desperdicio y crear un plan de acción para eliminarlo dentro del proceso.
A continuación se exhiben algunos estudios sobre la aplicación de la herramienta Value Stream Mapping en diferentes escenarios, con lo cual se valida su amplia aplicabilidad.
Haefner, Kraemer, Stauss, & Lanza (2014) presentan un enfoque innovador llamado Calidad del Mapeo de flujo de valor (QVSM), el cual es creado sobre la base de los elementos de diseño de VSM. La metodología generada por los autores proporciona una adecuada visualización, análisis y diseño de medidas de garantía de calidad dentro de las cadenas de procesos de fabricación. La herramienta es utilizada a modo de ejemplo para una compleja cadena de valor de un fabricante de la industria electrónica, en donde se logra optimizar la calidad de producto de múltiples estaciones de producción.
Brown, Amundson, & Badurdeen (2014) elaboran un Value Stream Mapping sostenible mediante la identificación de las métricas adecuadas y métodos para visualizarlos, enfocándose no solamente al impacto ambiental y económico sino también a la dimensión social; todo esto con el objetivo de desarrollar mejores estrategias para la producción sos-tenible. Asimismo, Edtmayr, Sunk, & Sihn (2016) combinan algunos parámetros de sostenibilidad con el mapeo de cadena de valor, con el propósito de identificar y reducir los recursos de consumo utilizados en los buffers, transporte y procesos a través de las actividades de la cadena de valor.
Azizi & Manoharan (2015) diseñan un Value Stream Mapping para mejorar la productividad en unas pequeñas y medianas empresas a través de la eliminación de actividades que no agregan valor al producto. Los autores utilizan un caso aplicado a una empresa productora de equipos electrónicos, la cual tenía altos tiempos y costos de producción. Al final del estudio, con la aplicación de la herramienta, se logra reducir el desperdicio y mejorar la calidad, mientras el tiempo y los costos de producción son reducidos.
Morlock & Meier (2015) desarrollan una adaptación del modelo de mapeo de cadena de valor para una empresa de servicios, logrando mejorar la efectividad de sus procesos, con lo cual se comprueba que la herramienta es funcional en todo tipo de escenarios de la vida real.
Rohac & Januska (2015) demuestran la aplicabilidad del método de Value Stream Mapping para la visualización y racionalización de procesos en el contexto real empresarial, para cumplir con este propósito, los autores aplican la metodología a una empresa de producción de plásticos que trabaja para la industria del cuidado de la salud. Los autores concluyen que con ayuda del VSM es posible generar pequeñas y continuas mejoras de carácter operativo; además de esto se pueden generar proyectos estratégicos que lleven al cumplimiento de los objetivos y la misión de la compañía.
Mohd & Mojib (2015) diseñan un mapeo de cadena de valor para una industria de colores, con el objetivo de determinar y eliminar los residuos que no agregan valor al producto final. Al término del estudio, luego de la implementación de la herramienta, se logra reducir el tiempo de producción de 8,5 a 6 días.
Tyagi, Choudhary, Cai, & Yang (2015) exploran conceptos de pensamiento lean con el propósito de gestionar, mejorar y desarrollar productos de una forma más rápida mientras se mantiene el mismo nivel de desempeño y calidad. Para este fin, los autores aplican la herramienta de Value Stream Mapping en la dependencia de investigación y desarrollo de una compañía, para la cual se logra reducir el tiempo de diseño de nuevos productos en un 50% luego de la imple-mentación de los planes generados a través del mapeo de cadena de valor.
Sa'udah, Amit, & Ali (2015) utilizan la herramienta de Value Stream Mapping para simular y ver el impacto que tiene el rediseño físico de la planta antes de su implementación y de esta forma seleccionar aquella opción que cumpla con los requisitos exigidos y a su vez genere el menor costo.
La intención del presente documento es proponer e implementar estrategias de mejora en el proceso logístico generadas por la aplicación de la herramienta de mapeo de cadena de valor. El artículo se encuentra distribuido de la siguiente forma: en la sección 2 se presenta el planteamiento del problema del caso de estudio en particular; en la sección 3 se expone la metodología utilizada para la aplicación de la herramienta de mapeo de cadena de valor y se termina exponiendo las principales conclusiones en el apartado 4.
1. Planteamiento del problema
Value Stream Mapping o mapeo de cadena de valor (VSM) es una herramienta de gestión Lean Manufacturing que utiliza símbolos, métricas y flechas para mostrar y mejorar el flujo de inventario y de información requerida para generar un producto o servicio que se entrega a un consumidor, buscando que este solo pague las actividades que le generan valor al producto.
El caso de estudio a ser analizado consiste en una empresa maquiladora2 que se dedica al empaque de todo tipo de cristalería tales como copas, vasos, platos, ensaladeras, licoreras, etc. La compañía actualmente empaca tres presentaciones distintas: estuches, avisperos y canastillas (Ver Figura 1).
Para cumplir con este objetivo utiliza tres insumos principales: el vidrio, que es cada artículo que va a ser empacado y el cual es proporcionado por la fábrica; el corrugado, que representa la cartonería necesaria para el determinado reempaque; y los códigos de barra, que son la forma como se identifican las referencias dentro del sistema de información del cliente (Ver Figura 2).
En el presente estudio se abordó el proceso de recepción, unificación, almacenamiento y alistamiento de corrugado debido a la inexactitud entre el inventario físico y el virtual que se estaba generando en cada una de las etapas del proceso, ocasionando constantes paradas en la producción por falta de corrugado y a su vez un nivel de servicio bajo para el cliente final. Ese desajuste en el inventario de corrugado provoca actividades de reproceso que consumen un mayor tiempo de lo requerido, por lo tanto se convierten en actividades que no genera valor agregado al producto.
En este estudio se hace necesaria la aplicación del Value Stream Mapping ya que es una herramienta que permite reconocer el estado actual del proceso, y con base en este proponer mejoras que conlleven a un funcionamiento ideal del sistema, donde las actividades que generen desperdicio dentro del proceso sean mínimas y solo queden aquellas tareas que le den un valor agregado al producto por el cual el cliente sí esté dispuesto a pagar.
2. Metodología
En el presente estudio, se utilizará la herramienta de Value Stream Mapping (VSM) para identificar las oportunidades de mejora dentro del proceso de recepción, unificación, almacenamiento y alistamiento de corrugado. Para desarrollar la técnica se tomarán como referentes los pasos realizados por Barcia y De Loor (2007), los cuales son mostrados en la Figura 3.
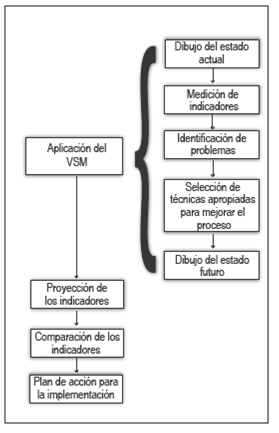
Fuente: Imagen tomada de Barcia y De Loor (2007).
Figura 3 Proceso metodológico de la herramienta Value Stream Mapping
Paso 1: Dibujo del estado actual
Se debe aclarar que el primer paso que definen los referentes es la construcción de un VSM que bosqueje la situación actual, mas no definen las actividades que se deben llevar a cabo para realizar este proceso; por tal motivo, para lograr desarrollar este primer punto se utilizarán las pautas del libro Mapping The Total Value Stream desarrollado por Nash y Poling (2008), la cual consiste en los pasos descritos a contunuación.
Levantamiento y descripción de las actividades que se realizan actualmente en el proceso
Como ya se había mencionado anteriormente, el corrugado es un insumo vital para el core business de Compañia, ya que sin esta materia prima no se podría entregar al cliente el producto deseado. Se debe aclarar que el proceso que se va a tratar en este documento es distinto, dependiendo del proveedor del cual llega la cartonería. Existen actualmente tres proveedores de este insumo: la planta de producción, la cual recibe parte del corrugado y lo envía a maquila; la bodega, es el lugar donde la planta de producción almacena toda su mercancía; y por último tenemos la situación en la que el proveedor directamente descarga el corrugado dentro de las instalaciones de la compañía. En este estudio se va a analizar particularmente el proceso que involucra la recepción de producto directamente del proveedor, ya que este implica una mayor complejidad para la organización.
El proceso que se abordó estaba dividido en cuatro fases o subprocesos: recepción, unificación, almacenamiento y alistamiento. Para describir cada una de estas actividades se llevó a cabo una entrevista con los encargados de cada tarea, con el objetivo de conocer cuál era el proceso que implicaba cada una de estas, para luego plasmarlo en un diagrama de flujo. A continuación se presenta la descripción de cada actividad del proceso:
Recepción: Esta actividad se inicia cuando el camión llega a la entrada de la bodega de la compañía, donde solo podrá ingresar si existe espacio disponible para descargar la mercancía, de lo contrario deberá esperar un tiempo para ser atendido. Una vez el vehículo se encuentra dentro de la bodega, el conductor deberá entregar la remisión3 al encargado del proceso de cartonería, el cual revisará si el producto que trae el camión pertenece a una referencia que programada para ser empacada. Si la mercancía sí se necesita, el encargado del proceso da la orden para comience el descargue del vehículo; en el caso de que haya llegado corrugado que no está programado para ninguna referencia, no se recibe y se debe devolver el camión a su lugar de origen.
En el proceso de descargue del camión, una persona está encargada de ir verificando que las cantidades que se encuentran dentro de la remisión sean las que realmente están siendo ingresadas a la bodega. Luego de esta actividad, la misma persona va estibando el corrugado y cada vez que termina una estiba, realiza un rótulo que contiene información básica de la cartonería que ha sido colocada dentro de esta, con lo cual se da finalización al proceso de recepción de cartonería.
Unificación: Esta actividad comienza una vez el corrugado ha sido recibido. Debido a que una referencia tiene varios componentes, por ejemplo: caja, división, avispero, etc.; y no todas las piezas llegan en un solo camión del mismo proveedor, la persona encargada de este proceso debe estar revisando continuamente qué componentes de cartonería van llegando de cada referencia para unificarlos en un solo lote y poderlos almacena.
Almacenamiento: Esta actividad es la más sencilla de todas, ya que lo único que se hace es verificar si existe espacio disponible en el área de almacenamiento, de ser así se ingresan las estibas con el corrugado; por el contario si no existe espacio, se almacena en un área temporal a la espera de un lugar en la estantería de almacenamíento.
Alistamiento: Esta actividad comienza con una revisión del Programa Maestro de Producción (PMP) por parte del encargado del almacenamiento; si la referencia va a ser programada para el día siguiente, se da la orden al montacarguista para que baje la estiba de la estantería de almacenamiento y la coloque en la zona de alistamiento, área en la cual el operario puede acceder directamente a la cartonería que necesite. En el caso de que la referencia no está programada para el día siguiente, se mantiene el corrugado dentro del área de almacenamiento
Estudio de tiempos de las actividades que involucra el proceso
Después de haber definido claramente el proceso, se procede a realizar un estudio de tiempos con el objetivo de identificar cuál es el tiempo de ciclo del corrugado dentro de la compañía. Antes de comenzar a realizar el estudio, se debe definir una unidad de medida para este, debido a que la cartonería que maneja la empresa es muy variable; por ejemplo, un día pueden llegar 10 cajas y al otro, pueden arribar 1.000. Esta unidad de medida también será con la que se construirá el VSM actual de la compañía.
La estrategia desarrollada para encontrar esa muestra representativa de cartonería consistió en dos pasos principalmente: El primero estuvo fundamentado en la búsqueda de las referencias más programadas dentro del lapso del estudio, se utilizó como criterio de selección, aquellas referencias que habían sido programadas más de 20 veces. Como las referencias no son programadas siempre en la misma cantidad, se calculó un promedio de cajas con base en el total de cajas y al número de veces que había sido programada. El segundo paso consistió en identificar qué componentes tenía cada referencia, mediante la utilización de la lista de materiales (Bill of Materials, BOM) y luego ver cuántas piezas se necesitaban para cumplir con el promedio de cajas previamente calculado. La Tabla 1 muestra los resultados de este proceso
En la Tabla 1 se puede observar que para la muestra representativa solo se seleccionaron las referencias de cada presentación que más rotación habían tenido en el lapso de la investigación (resaltadas por la línea azul oscura). Con base en esta información se determinó la unidad de medida del estudio de tiempos y el VSM de la siguiente manera:
Una vez se tiene la muestra representativa con la cual se va a realizar el estudio de tiempos, se procede a definir las tareas de cada uno de las actividades que implica el proceso objeto de estudio. Luego de esto se pasa a calcular el tamaño de muestra para cada tarea con base en el método estadístico propuesto por la Orgánización Internacional del Trabajo. El método estadístico consiste en efectuar un cierto número de observaciones preliminares (n') y luego aplicar la fórmula (ecuación 1) para un nivel de confianza de 95,45% y un margen de error de 5%.
Ecuación 1. Fórmula para calcular tamaño de muestra Donde:
n= Tamaño de muestra que se desea determinar
n'= Tamaño de muestra preliminar
X= Valor de las observaciones
Para el caso de estudio se estableció una muestra preliminar de cuatro observaciones para cada tarea y con ayuda de la ecuación 1, se procedió a calcular el tamaño de muestra de cada elemento de las cuatro fases del proceso previamente definidas (Para ver los resultados diríjase al Anexo A) Luego se procede a estimar el tiempo que se demora la muestra representativa en pasar por todo el proceso, teniendo en cuenta el ritmo al cual trabaja el operario y un tiempo de suplemento basado en las condiciones del ambiente y trabajo. Luego de esto se establece el tiempo tipo de cada una de las fases del proceso y con estos valores se calcula el tiempo de ciclo de la muestra representativa, el cual es equivalente a 359,9 minutos.
Después de haber determinado el tiempo que se demora la muestra representativa en pasar por todas las etapas del proceso, se procede a realizar el trazado del Value Stream Mapping de la situación actual. Para cumplir con este objetivo se utiliza una versión gratuita limitada de un software llamado eVSM, el cual permite realizar el trazado de mapas de cadena de valor, usando programas como Microsoft Excel y Microsoft Visio Professional. En este software se logra consolidar el estudio de tiempos y la definición de actividades del proceso para crear así el mapa de cadena de valor actual.
En la Figura 4 se muestra el VSM actual.
En este se puede observar cómo la planta de producción es la entidad de control del sistema, ya que es la encargada de emitir las órdenes de compra a los proveedores de cartonería, y a su vez, programar las referencias a las líneas de empaque, el cual es el cliente del proceso.
El mapa de la cadena de valor refleja el comportamiento del sistema: se puede notar cómo cuando las órdenes de compra llegan a los proveedores, estos envían el pedido a la bodega, teniendo en cuenta que se debe asumir una espera para poder ingresar a esta.
Una vez que el vehículo logra entrar a la empresa, comienza el proceso de recepción, y en caso de que no todos los componentes lleguen juntos, la cartonería se convierte en inventario en proceso en busca de entrar a la fase de unificación.
Luego de que la mercancía ha sido unificada, esta se traslada al proceso de almacenamiento y una vez que es programada la referencia en la cual va a ser utilizada, el corrugado llega a la última etapa del proceso: el alistamiento, lugar en el cual los operarios de la línea de empaque pueden acceder a la cartonería sin ningún problema.
Paso 2: Medición de indicadores
Para determinar el estado de la situación actual se debe primero aclarar y explicar tres conceptos fundamentales, los cuales son:
Capacidad efectiva: Es la capacidad que una empresa espera alcanzar dadas las restricciones de operaciones existentes. A partir de este indicador, se calcula la eficiencia del proceso.
Tiempo de ciclo: Es el tiempo promedio entre la producción de dos unidades consecutivas
Tiempo takt: Es el máximo tiempo de ciclo permitido para producir un elemento y poder cumplir la demanda. La situación ideal es que el takt time sea igual al tiempo de ciclo, de lo contrario se puede incurrir en costos de faltantes o sobreproducción.
Luego de explicados estos conceptos, se procede a analizar los resultados arrojados de la simulación del estado actual hecha mediante el software eVSM. En la Figura 5 se puede notar cómo las etapas de almacenamiento y alistamiento son las menos eficientes del proceso, ya que son las que tienen menos capacidad. Asimismo, en la Figura 6 se puede evidenciar cómo el tiempo de ciclo es mucho menor al tiempo takt, lo que refleja que el proceso está respondiendo lentamente a las necesidades que está exigiendo el cliente, por lo que se está generando un nivel de servicio bajo y se está haciendo necesaria la implementación de actividades de reproceso para poder cumplirle al cliente. En conclusión, los resultados de simulación de la situación actual reflejan un comportamiento indeseable del sistema, donde se está teniendo un nivel de servicio bajo y a la vez se están desperdiciando recursos de espacio, tiempo y dinero.
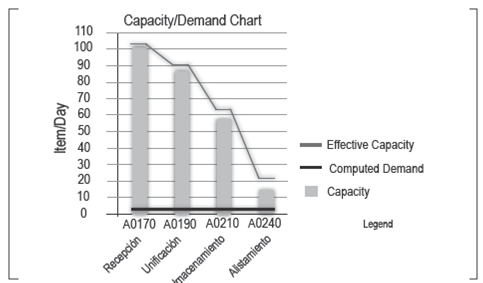
Fuente: El autor
Figura 5 Capacidad efectiva de las etapas del proceso de recepción, unificación, almacenamiento y alistamiento de corrugado
Paso 3: Identificación de problemas en el proceso actual
El estudio de tiempos no solo se convirtió en una herramienta para medir el tiempo de ciclo del proceso, sino que también se consolidó como una forma de ver todo el sistema y poder encontrar oportunidades de mejora dentro de este. Luego de la observación del proceso, se encontraron cuatro problemas principales que afectaban el desempeño del sistema. A continuación se menciona cada uno de estos:
Carencia de un sistema de control de inventario de estibas y láminas en la etapa de recepción
Cuando se estaba realizando la toma de tiempo para el estudio, se logró evidenciar un hecho, en la etapa de recepción, que se repetía continuamente: la persona que descargaba la cartonería se quedaba sin estibas y láminas, lo que provocaba que este parara el proceso para recorrer la bodega en busca de estos insumos tan necesarios para esta etapa. Falta de un área definida para el almacenamiento temporal de corrugado
Como ya se había comentado, la cartonería que no llega completa, se deja en un lugar a espera de que los componentes que faltan arriben a la bodega. El problema consiste en que esta área de almacenamiento temporal es seleccionada aleatoriamente y no tiene un lugar fijo dentro de la bodega, lo que ocasiona desorden y movimientos innecesarios para el operario encargado de la fase de unificación.
Carencia de un montacargas disponible para el proceso
Actualmente la empresa cuenta con dos montacargas: uno encargado del surtido de vidrio a las líneas y otro que provee despacho de producto terminado. Debido a que el proceso involucra movimiento constante de estibas, es necesario que un montacargas preste continuamente su servicio a este proceso, para evitar esperas innecesarias de traslado de estibas de un lugar a otro.
Falta de comunicación entre las dependencias de la compañía
Por último, se logró identificar que la empresa tiene un déficit de comunicación entre sus dependencias, por lo que muchas veces lo que sucede en el área de producción no es informado al proceso de cartonería y esto provoca actividades de reproceso que se podrían evitar simplemente teniendo intercomunicada toda la compañía.
Paso 4: Selección de técnicas apropiadas para mejorar el proceso
Para cumplir con este paso, se empleó la misma metodología utilizada por Barcia y De Loor (2007), los cuales usaron una tabla donde se especificaba el problema, el tipo de desperdicio que este involucraba y la técnica que ayudaría a solucionarlo.
En la Tabla 3 se presentan dichas características, en las cuales se puede notar lo siguiente: para el primer problema planteado se va implementar un sistema de control kanban, buscando reducir el desperdicio generado por la ausencia de este inventario; para mejorar el segundo problema, en el cual existe un desperdicio en los movimientos del operario, se ejecutará un plan de 5S y luego un estudio de capacidad y distribución de la bodega; para el tercer problema, se buscará dar una capacitación a los montacarguistas para que le presten su servicio al proceso y por último, para mejorar la comunicación entre las dependencias de la compañía se efectuará un trabajo conjunto de los jefes de las áreas con el objetivo de establecer una red de intranet para la compañía.
Paso 5: Mapeo de la cadena de valor de la situación futura
Luego de identificar las soluciones a los problemas que se presentan dentro del proceso, se pasa a plasmar dichas técnicas en el mapa de la cadena de valor, con el objetivo de simular el comportamiento ideal del sistema y compararlo con los indicadores actuales.
En la Figura 7 se puede observar cómo la primera mejora a establecer es la ejecución de un sistema de control kanban para las estibas y láminas, la cual buscará reducir los desperdicios asociados a la etapa de recepción.
Asimismo en la Figura 8 se nota cómo un proyecto de distribución en planta puede mejorar el desempeño de las fases de unificación, almacenamiento y alistamiento.
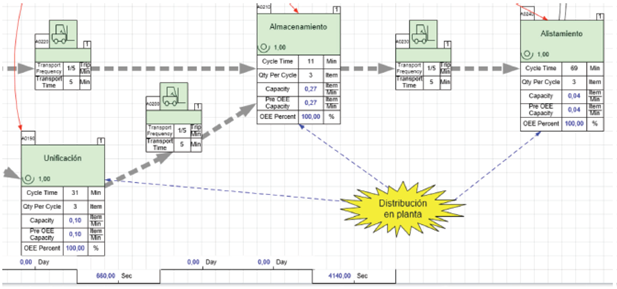
Fuente: El autor
Figura 8 Establecimiento de un proyecto de distribución en planta para el proceso base.
Por último, en la Figura 9 se evidencia la aplicación de las dos últimas mejoras propuestas para el proceso en cuestión: lá capacitación de montacargas que implica un transporte más eficiente de recursos y el sistema de información que intercomunique a todas los encargados del proceso.
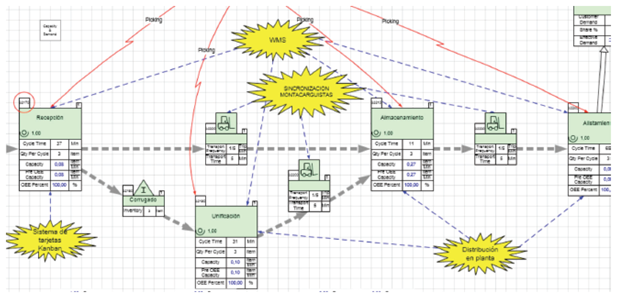
Fuente: El autor
Figura 9 Ejecución de la capacitación de montacargas y el sistema de información dentro del proceso base
La aplicación de las técnicas propuestas dentro del mapa de cadena de valor crea una situación futura óptima, la cual consolida la última fase de la metodología aplicada y es llamada Value Stream Mapping futuro (Ver Figura 10).
Paso 6: Proyección y comparación de indicadores
Una vez se tiene plasmada la situación ideal se procede a realizar la simulación del sistema y a compararlo con el proceso actual. Se debe tener en cuenta que las fases del proceso se identifican en los gráficos a través de una numeración ascendente, donde 1 es la primer etapa y 4 es la última. En la Figura 11 se evidencia cómo el tiempo de ciclo de la muestra representativa es menor en la situación futura, ya que en este escenario se logran eliminar aquellas actividades que generaban desperdicio de tiempo en el proceso y por ende no agregan valor al producto.
De igual forma, se debe resaltar cómo todas las fases del proceso aumentan su capacidad efectiva (Ver Figura 12), es decir, ahora en el mismo tiempo se logra llevar una muestra de corrugado más grande al cliente, que en este caso es la línea de empaque, lo que hace que la eficiencia del proceso aumente.
Paso 7: Establecimiento del plan de acción
Luego de confirmar que las técnicas a ser aplicadas dentro del proceso pueden mejorar el desempeño de este, se procede a definir un posible plan de implementación de estas. A continuación se explicas las mejoras que se lograron implementar dentro del proceso
Aplicación de las 5S a la bodega de insumos
Para la implementación de esta técnica se dispuso de un día donde no había labor de empaque, todo con el objetivo de clasificar, organizar y limpiar toda la bodega. Al final de este proceso se delimitó un área para cartonería y para vidrio; además se implementó un programa de limpieza para los encargados del proceso, con el objetivo de comprometer a las personas a mantener un lugar de trabajo limpio y ordenado.
Implementación de sistema kanban para el control del inventario de estibas
Para la ejecución de esta mejora se comenzó con la idea de colocar un número determinado de tarjetas en las estibas y cada vez que una de estas se utilizara, sacar la tarjeta de la estiba y dejarla en un lugar prefijado, para que la persona encargada del proceso de cartonería repusiera las estibas equivalentes al número de tarjetas que estaban sueltas. Se implementó esta idea pero surgió el problema de que dichas fichas de cartulina se caían de la estiba, antes de ser utilizadas, lo que ocásionaba un descontrol en el inventario de estibas, ya que no todas las tarjetas sueltas representaba una situación en la que se debían reponer estibas.
Al fracasar esta idea, se pasó a proponer una forma diferente para el control de inventario de este insumo: Se iba a calcular el inventario máximo y mínimo de estibas necesarias para todo el proceso de la compañía (incluyendo despacho y área de producción). Luego de esto, se iban definir tres límites: inventario máximo, inventario mínimo y punto de reorden. Para hacer más fácil la identificación del momento en el que se debe pedir, se pasaría entonces a colorear el piso del área destinada para el almacenamiento de este insumo: el color verde representaría el hecho de que hay suficientes estibas para cumplir con todos los procesos normales de la compañía; el color amarillo implicaría llevar un seguimiento riguroso del inventario, ya que es una alerta de que en cualquier momento se debe pedir; por último, el color rojo representaría la situación en la cual el encargado del proceso de cartonería debe pedir las estibas a la planta. Esta propuesta fue aprobada por la gerencia y actualmente se encuentra en proceso de ejecución.
El indicador que se utilizó para medir el impacto del estudio sobre el desempeño de la compañía fue el dinero gastado en horas extras para el proceso de cartonería, ya que estas representan un tiempo de reproceso que se debe eliminar para agregar valor al producto. En la Tabla 4 se puede notar cómo, antes de que se implementaran las mejoras, la empresa llegó a gastar hasta $1.298.768 en un mes para cubrir actividades de reproceso en el área de cartonería. La implementación de las propuestas eliminó las horas extras en el proceso de recepción, unificación, almacenamiento y alistamiento de empaque, lo que evidencia el impacto de las mejoras en la compañía a través de un ahorro en tiempo, que implica que el cliente no está pagando por una actividad que no le agrega valor a su producto.
Conclusiones
La implementación de la herramienta de Value Stream Mapping permitió mostrar a la alta gerencia cómo se desempeñaba uno de los procesos más críticos dentro de la compañía y con esa base ver el comportamiento de todo el sistema de una forma global y no por partes. Al identificar el comportamiento y las relaciones subyacentes dentro del proceso, se logró establecer un plan de acción que actualmente se encuentra en ejecución y que en corto tiempo ha entregado ahorros considerables a la compañía.
Además, las mejoras propuestas se han convertido en herramientas fáciles de aprender y que les han mostrado a los encargados del proceso cómo debe ser la manera correcta en la que debe funcionar el sistema y cuál es la forma de actuar en ocasiones de crisis.
Entre las técnicas desarrolladas y que han evidenciado excelente resultados se encuentra la aplicación de un sistema de 5S con lo que se logró tener una bodega limpia y ordenada. Asimismo se espera que la idea de controlar el inventario de estibas a través de franjas de colores tenga un efecto positivo en los encargados del proceso y provoque un ahorro en tiempo y dinero para la compañía.