Introducción
El cambio de los procesos industriales durante la revolución industrial desencadenó un incremento en las concentraciones de gases de efecto invernadero como el CO2. Anteriormente, la concentración de este gas oscilaba entre 200 y 280 partes por millón, pero en noviembre de 2014 llegó a un tope de 398 partes por millón y se espera que alcance las 800 partes por millón a finales de siglo. (Salas et al., 2016). Una de las causas del alza de esta concentración es la expansión del número de estructuras construidas a partir del concreto, el conglomerado de empresas dedicadas a la construcción mueve aproximadamente el 10 % de la economía mundial y consume cerca del 40 % de la energía que es generada en todo el planeta (Cardim De Carvalho Filho, 2001). A su vez, esta requiere de la industria del cemento. El cemento es un aglutinante muy antiguo que ha servido en la construcción desde el imperio romano. Sin embargo, no fue sino después de la Segunda Guerra Mundial que la producción de este material cementante tuvo un auge de producción global (Andrew, 2018), este material tiene beneficios como la facilidad de manejo, su alta resistencia a la compresión y un bajo costo en contraste con otros materiales. Aun así, y con todas las ventajas que ofrece, la industria concretera es causante de entre el 7 y el 8 % de las emisiones globales de gases de efecto invernadero. (Andrew, 2018) (Al-Safy, 2015). Debido a que se requiere el aprovechamiento de toneladas de roca y arena para la producción del concreto, como resultado, se requieren entre 1,1 a 1,5 toneladas de recursos naturales para producir 1 tonelada de este producto (Al-Safy, 2015) (Alfocea Roig, 2020). De igual forma, se necesitan procesos de incineración para la producción del cemento Portland, los cuales demandan grandes montos de energía., aproximadamente el 2 % de la energía que se produce en el planeta se consume en la producción del cemento (Alfocea Roig, 2020).
Como resultado, debido al uso de cemento Portland, se generó a nivel global cerca de 36 Gt de CO2 en 2013, un aumento de alrededor del 2,3 por ciento si se compara con el año 2012, y un aumento del 61 por ciento comparándolo con la generación de CO2 en 1990. (Salas et al., 2016). A su vez, en el 2018 las cementeras fueron la segunda industria en producir mayores emisiones de CO2 en el mundo, y fue la tercera industria en mayor consumo energético en el mismo año (Alfocea Roig, 2020). A pesar de esto, el CO2 no es el único problema causado por las empresas productoras de cemento; el procesamiento industrial y la minería son unas de las fuentes causantes de contaminación por metales en el medio ambiente. La industria del cemento también es responsable de un incremento de los factores causantes de cáncer, que en su mayoría son originados en los procesos de producción de energía y en el uso de combustibles fósiles. Asimismo, la mala gestión de los residuos generados en esta industria, así como el excesivo aprovechamiento de las canteras, repercute negativamente en la calidad del suelo, imposibilitando su aprovechamiento por décadas. (Salas et al., 2016).
A su vez, el hormigón elaborado con cemento Portland es el material de construcción más utilizado a nivel global. Aunque existen muchos otros tipos de cemento, el conocido como Portland es el más utilizado de todos ellos, este fue inventado por Joseph Aspdin en 1824 y lleva el nombre de los acantilados de calciza de la isla de Portland en Inglaterra. (Mamlouk & Zaniewski, 2009) La producción de este cemento comienza con dos ingredientes básicos que son un material calcáreo y otro arcilloso. El material compuesto de calcio está formado por un óxido de calcio al igual que la piedra caliza, conchas de ostras y caracoles o como el yeso, por otro lado, el material compuesto de arcillas es una mezcla de silicio y aluminio extraíbles a partir de suelos arcillosos, escorias de alto horno o esquistos. Los materiales deben ser molidos y guardados antes de ser enviados a un horno principal donde serán horneados a temperaturas entre 1400°C y 1650°C donde se funden (Viandy et al., 2018), esto es lo que convierte estos materiales en Clínker de cemento. Paso siguiente, el Clinker se muele para obtener un fino polvo, al que se le agrega un pequeño porcentaje de yeso con el fin de controlar el tiempo de fraguado del cemento. (Mamlouk & Zaniewski, 2009) (Hewlett & Liska, 2019).
Cal, sílice, óxido de aluminio y óxido de hierro, son los principales compuestos químicos que conforman el cemento tipo Portland. Durante la calcinación se reestructura la composición molecular, por lo que los materiales bases generan productos químicos de alta complejidad, dichos productos se muestran en la Tabla 1 (Viandy et al., 2018).
Tabla 1 Principales compuestos químicos del cemento tipo Portland.
Compuesto | Fórmula química | Fórmula común | Rango usual en peso (%) |
---|---|---|---|
4CaO | |||
Ferroaluminato tetracálcico | - Al 2 O 3 | C 4 AF | 6-8 |
- Fe 2 O 3 | |||
Aluminato tricálcico | 3CaO | C 3 A | 6-12 |
- Al 2 O 3 | |||
Silicato dicálcico | 2CaO | C 2 S | 15-30 |
- SiO 2 | |||
Silicato tetracálcico | 3CaO | C 3 S | 45-60 |
- SiO 2 |
Fuente: Tomada de Mamlouk y Zaniewski, 2009.
Las empresas dedicadas a la construcción han evolucionado de tal manera que ahora se enfrentan a nuevos desafíos de ingeniería donde ven necesario nuevos materiales con diferentes características, lo que ha llevado a los fabricantes de cemento a desarrollar una variedad de tipos de cemento para producir concreto con diversas especificaciones. La Tabla 2 resume los principales tipos de cementos y sus aplicaciones.
Tabla 2 Tipos de cementos existentes.
Tipo | Nombre | Aplicación |
---|---|---|
I | Normal | Se utiliza cuando no se requieren propiedades específicas en el concreto; es el más ampliamente usado. |
II | Resistencia media a sulfatos | Protección media a sulfatos, entre 0.1-0.2 porciento de peso de sulfatos solubles en agua, en suelos o 1500-10800 partes por millón de sulfatos en agua; utilizado en la construcción de muelles y muros de contención. |
III | Elevada resistencia inicial | Se usa cuando se deben retirar rápidamente los encofrados o se debe poner en funcionamiento la estructura lo antes posible, se utiliza en construcción rápida. |
IV | Bajo calor de hidratación | Es requerido para construcciones con grandes dimensiones, en donde debido al tamaño el calor de hidratación en considerable y conlleva a problemas en el fraguado y curado del concreto |
V | Elevada resistencia a sulfatos | Protege en casos de exposición alta a sulfatos, entre 0.1-2 porciento de peso de sulfatos solubles en agua, en suelos o 1500-10800 partes por millón de sulfatos en agua |
Fuente: Tomada de Mamlouk y Zaniewski, 2009.
Desde el año de 1970, el conglomerado de la construcción ha utilizado una variedad de subproductos de otras industrias como aditivos en el cemento, con el fin de mejorar una o más propiedades del concreto. Entre ellos, se encuentran las escorias de horno alto molidas, el humo de sílice, el polvo de ceniza y las puzolanas naturales; estas adiciones producen principalmente un cemento hidráulico no metálico compuesto básicamente de silicatos y aluminosilicatos de calcio, estos reaccionan químicamente con el hidróxido de calcio a temperaturas normales para formar compuestos que presentan propiedades cementosas (Hewlett & Liska, 2019). El futuro de las investigaciones se visiona en la utilización de residuos sólidos urbanos, industriales y agroindustriales, ya que el enfoque de la ciencia hoy en día está basado en sustituir la materia prima para la elaboración del cemento con residuos de otras industrias, de esta forma se busca reducir el costo necesario para la elaboración de dicho producto requerido en la construcción, y a su vez reincorporar dentro de la cadena de producción sobrantes considerados como desechos (Viandy et al., 2018). Las recientes investigaciones han demostrado que desechos tales como fibras naturales o de acero, cenizas volantes, silicona, humo de sílice, vidrio, caucho triturado, y desechos de ciertas industrias. Tal como es el objeto de este estudio, la cáscara de huevo y la cascarilla de arroz. La primera ha despertado el interés de países productores de huevos, como India y Malasia, donde este desecho se ha convertido en una preocupación ya que puede convertirse en un alérgeno para muchas personas cuando pasan mucho tiempo en los botaderos. (Akhil & Kumar, 2015), Todo esto combinado, los malos olores que producen este tipo de desechos, la cáscara de huevo se convierte en un material deseable para la fabricación de materiales compuestos ya que resuelve una variedad de problemas y además es un material sencillo y, en muchos casos, gratuito de obtener. Por otro lado, la cáscara de arroz es considerado un subproducto del mercado global del arroz, el cual tuvo, según la FAO, una producción mundial calculada de 756.7 millones de toneladas durante el 2017 (FAO, 2017). Adicionalmente, al calcinar este desecho se obtiene un material Puzolánico que es usado ampliamente en procesos industriales para la fabricación de concreto, cerámicas, aislantes, etc. (Vidal et al., 2018).
En el caso de la cáscara de huevo (CH), y su producto de consumo (el huevo), es considerado un alimento básico en la canasta familiar de cualquier colombiano y ciudadano del mundo, es un producto rico en proteínas y minerales que es ampliamente utilizado en la industria alimenticia, incluyendo restaurantes, pastelerías y panaderías, entre otros lugares. Según FENAVI, el colombiano promedio se alimenta de alrededor de 252 huevos por año, lo que genera más de 13 millones de cáscaras de huevo en Colombia. (Valencia, 2016), estas son desechadas sin generar un valor agregado y son depositadas en botaderos donde su descomposición genera malos olores y lixiviados difíciles de tratar.
Una cáscara de huevo de buena calidad contiene alrededor de 2,2 gramos de calcio en forma de carbonato de calcio, este compuesto ronda entre el 94 y el 97 % de la composición de la cáscara, mientras que el restante 3 % es normalmente materia orgánica y pigmentos como fósforo, magnesio, potasio, zinc, manganeso, hierro y cobre. En la Tabla 3 se puede apreciar la composición de la cáscara de huevo. El color, la forma y la estructura de la cáscara de huevo determinan la calidad del producto. Los colores pueden variar de blanco a marrón oscuro, y la forma del huevo también puede cambiar. (Hassan, 2014).
Tabla 3 Composición química de la cáscara de huevo. Tomada de Hassan, 2009.
Composición química de la CH | Contenido (%) |
---|---|
CaCO 3 | 94 |
MgCO 3 | 1 |
Ca 3 (PO 4 ) 2 | 1 |
Materia Orgánica | 4 |
Investigadores (Cree & Rutter, 2015) se han focalizado en el uso de la CH incineradas porque producen un compuesto químico conocido como óxido de calcio o más comúnmente conocido como cal viva, que fue ampliamente utilizado en el pasado. (Cree & Rutter, 2015); a la hora de hidratar, este elemento actúa como aglutinante, transformándose en una pasta de hidróxido de calcio que une los elementos a su alrededor. Esta información se muestra en la Tabla 4 con la composición de la cáscara de huevo químicamente luego de un proceso de incineración a 500°C (CCH), lo cual reduciría gastos energéticos en la producción del cemento, ya que para la producción del cemento tipo Portland, requiere temperaturas superiores a los 1000°C (Mamlouk & Zaniewski, 2009).
Tabla 4 Composición química de la cáscara de huevo incinerada a 500°.
Composición Química de la CCH | Porcentaje en peso |
---|---|
CaO | 50.7 |
SiO 2 | 0.09 |
Al 2 O 3 | 0.03 |
Fe 2 O 3 | 0.02 |
MgO | 0.01 |
Na 2 O | 0.19 |
SrO | 0.13 |
NiO | 0.001 |
P 2 O s | 0.24 |
SO 3 | 0.57 |
Cl | 0.08 |
Pérdidas por incineración | 47.8 |
Fuente: Tomada de Hassan, 2009.
Estudios llevados a cabo en India y Malasia sobre el uso de la cáscara de huevo como material de reemplazo del cemento Portland muestran que los morteros de hormigón con porcentajes de reemplazo bajos (menos del 5 %) se comportan de manera similar a los morteros de hormigón sin reemplazo en pruebas de compresión y flexión (Al-Safy, 2015; Karthick et al., 2014; Yerramala, 2014). Por lo que existe una viabilidad comercial limitada debido a los bajos porcentajes de reemplazo, lo que se traduce en pocos costos reducidos.
Por otro lado, la cascarilla de arroz es un residuo generado durante la obtención del arroz, existen actualmente 22 especies del género Oryza en el mundo, de las cuales solo dos son cultivadas para el consumo humano, Oryza sativa y Oryza glaberrima (Jhatial et al., 2019). Actualmente el arroz es cultivado en todos los continentes exceptuando la Antártida. Según un informe de la FAO, durante el año 2017 la producción de arroz alcanzó una cifra récord de 759,6 millones de toneladas producidas y en Colombia en ese mismo año la producción alcanzó la cifra de 2.7 millones de toneladas.
Diferentes autores han analizado la composición química de la cascarilla de arroz con el fin de identificar opciones de aprovechamiento, la Tabla 5 presenta los valores de dicha composición obtenida en los estudios más recientes.
Tabla 5 Composición química de la ceniza de cascarilla de arroz (CCA).
Compuesto De la CCA | (Rego et al., 2015) | (Swaminathen & Ravi, 2016) | (Mahmud et al., 2016) |
---|---|---|---|
Si O 2 | 87.08% | 87.2% | 85.76% |
Al 2 O 3 | 0.01% | 0.15% | 0.25% |
Fe 2 O 3 | 0.11% | 0.16% | 1.15% |
CaO | 0.70% | 0.55% | 0.74% |
MgO | 0.42% | 0.35% | 0.81% |
Na 2 O | 0.18% | - | - |
(SO 3 ) | - | 0.24% | 0.31% |
P 2 O 5 | - | - | - |
K 2 O | 1.40% | - | - |
Fuente: Tomada de A. Jhatial, W. Goh, K. Mo, et al. 2019.
Así mismo, diversos autores han utilizado ambos componentes, la cáscara de huevo (CH) y la cascarilla de arroz (CA) en conjunto como reemplazo de material cementante (Asman et al., 2017; Jhatial et al., 2019; Siddiq & Tay, n.d.; Soumyan & Viswanath, n.d.). Estas combinaciones se dan debido a que la CH posee un gran porcentaje de calcio, lo que se asemeja a la composición del cemento. Sin embargo, esta no permite alcanzar las resistencias a compresión obtenidas por un cemento Portland tradicional (Asman et al., 2017), por lo que es necesario agregar otro componente que logre aportar el óxido de sílice que le brinda parte de la resistencia del material, como es el caso de la cascarilla de arroz. Además de aportar el beneficio ya mencionado, la CA mejora la reactividad de la hidratación, al proveer una superficie más grande para la reacción. De igual forma, esta puede aportar a la resistencia a la flexión y a la durabilidad del concreto (Soumyan & Viswanath, n.d.). Por lo que analizando los resultados obtenidos por las diferentes investigaciones, se evidencia que un porcentaje de reemplazo de 14 % de CH y 5 % de CA es la combinación óptima para estos materiales, ya que estos porcentajes mostraron los mejores resultados de los estudios realizados (Siddiq & Tay, n.d.).
Debido a estos beneficios ofrecidos, se decide combinar tanto la cáscara de huevo como la cáscara de arroz para obtener un nuevo material cementante que busca combinar los beneficios del carbonato de calcio obtenido del primero y la sílice obtenida del segundo. De igual forma, para determinar la viabilidad ambiental de este nuevo material, se debe evaluar su impacto al medio ambiente ocasionado al fabricar un cemento Portland con reemplazo de CH y de CA, y compararlo con el impacto ambiental generado por la fabricación de un cemento Portland tradicional. Para esto existen diferentes metodologías que permiten evaluar la nueva alternativa de reemplazo de material cementante, en este caso se utilizará el Análisis de Ciclo de Vida (ACV), ya que es una metodología que ha demostrado su eficacia para valorar los impactos potenciales sobre el medio ambiente. Esta ofrece la ventaja de ser una herramienta "desde la cuna hasta la tumba", lo que permite analizar todas las consecuencias medioambientales durante toda la etapa de un material (Cardim De Carvalho Filho, 2001). Con la finalidad de incorporar residuos nuevamente a la cadena productiva y disminuir la contaminación generada por la industria cementera, esta investigación tiene como objetivo realizar el análisis del ciclo de vida (ACV) de un cemento creado con un reemplazo de 14 % de cáscara de huevo y 5 % de cáscara de arroz, estas serán integradas como parte del proceso productivo actual, por lo que los procesos como molienda e incineración se mantendrán acorde a lo que existe actualmente. Esto con el fin de no generar traumas en los procesos actuales y que permitan generar una disminución en la cantidad de materiales provenientes de la minería y generar un rehusó a los residuos agroindustriales. De esta forma, se verificará las disminuciones de dióxido de carbono, así como todos los impactos generados por este nuevo producto.
Materiales y Métodos
Metodología.
El análisis del ciclo de vida (ACV) basado en la norma ISO 14040, es una herramienta fundamental para identificar y evaluar los impactos potenciales sobre el medio ambiente durante la vida útil de un producto, en este caso el cemento Portland con un reemplazo de 14 % de ceniza de cáscara de huevo y 5 % de cascarilla de arroz. El ACV es un proceso desde la cuna hasta la tumba, donde se analiza desde su producción, uso y desecho o rehusó (Song et al., 2016). Para esto la ISO 14040 define cuatro elementos:
Definir objetivos y el alcance, así como los límites del sistema.
Realizar el análisis del inventario
Evaluar los impactos del producto o tecnología.
Interpretar y analizar los resultados.
De esta forma y siguiendo la metodología usada por D. Song, J. Yang, B. Chen et al. Se definen los elementos anteriormente mencionados.
Definición de objetivo y alcance
Esta investigación tiene como objetivo el evaluar los impactos ambientales ocasionados por una cadena de producción de cemento Portland con un reemplazo de 14 % de cáscara de huevo y 5 % de cascara de arroz, de acuerdo con lo estipulado como viable en investigaciones anteriores (Viandy et al., 2018), manteniendo los procesos actuales de una planta tradicional de cemento Portland, como molienda e incineración con el mismo consumo energético, esto con el fin de facilitar la incorporación de estas adiciones sin cambiar los procesos tradicionales. La cantidad por evaluar es la producción de 1 tonelada de cemento. Cabe resaltar que para este análisis se debe realizar desde el punto de vista de la cuna hasta la tumba, entendiendo su nacimiento como el momento de su desecho. Ya que, con el reemplazo de cáscara de huevo y de cascarilla de arroz, su principal materia prima son materiales de desecho. Para el análisis completo se decidió utilizar 6 procesos como una simplificación de todos los procesos inmersos, estos son transporte, preparación de materias primas, calcinación, molienda, envasado y otros (ver Fig. 1).
Análisis del Inventario
Para el análisis del inventario se tuvieron en cuenta publicaciones similares (Cardim De Carvalho Filho, 2001) y bases de datos como la base de datos de Agribalyse v3.0.1, la cual es la base de datos francesa para el análisis de ACV del sector agrícola y alimentario, estas inmersas en el software a usar como es OpenLCA. Para esto el cemento con porcentaje de reemplazo de cáscara de huevo (14 % de reemplazo) y cascarilla de arroz (5 % de reemplazo) se requiere:
Cáscara de huevo y cascarilla de arroz.
Insumos energéticos de sistemas externos como el carbón y la electricidad.
Piedra Caliza, Arena y Yeso.
Transporte de materiales
Y generan ambos como salidas un cemento Portland con reemplazo de 14 % de CH y 5 % de CA (para 1 tonelada de cemento).
Transporte
Para la fabricación del cemento Portland con reemplazos de CH y CA, se utilizan camiones diésel pesados con una capacidad de transporte de 30 toneladas para el transporte de las materias primas. Para la obtención de la distancia, el análisis se realizó para una planta ubicada en la ciudad de Cartagena de indias, Colombia. En el caso de la cantidad transportada, se tuvo en cuenta un porcentaje de desperdicio de 1 % para todas las materias primas. La cantidad transportada se muestra en la siguiente tabla.
Tabla 6 Transporte de materias primas.
Transporte de materias Primas | |||
---|---|---|---|
Materias primas | Procedencia | Cantidad (Kg) | Distancia (Km) |
Piedra Caliza | Arroyo de Piedra, Atlántico | 1296 | 62.5 |
CH | Relleno sanitario | 150 | 15.7 |
CA | Magangué, Bolívar | 60 | 220 |
Arena | Arroyo de Piedra, Atlántico | 218.7 | 62.5 |
Yeso | Arroyo de Piedra, Atlántico | 60 | 62.5 |
Fuente: elaborado por autores.
Preparación de materias primas
Para la etapa de preparación de materias primas se tienen en cuenta procesos como la trituración, el premezclado y la molienda. En esta etapa, la electricidad se utiliza para conducir equipos de trituradora, transportador de cinta, apilador-recuperador, sistema de molino vertical y pulverizador de bolas. La electricidad consumida en esta etapa es de 196 MJ por tonelada de cemento (Cardim De Carvalho Filho, 2001).
Calcinación
En el proceso de calcinación del cemento Portland, la materia prima es preparada y se calienta en un precalcinador donde se inicia la oxidación de CaCO3 al óxido de calcio (CaO) y como producto residual se obtiene CO2. Después de esto, lo resultante se ingresa en un horno rotativo para continuar la reacción entre el CaO y otros elementos para formar silicatos de calcio y aluminio. La salida del proceso es el clinker, el cual es entregado para que repose hasta temperatura ambiente. La energía consumida en este proceso es de 3380 MJ por tonelada de cemento (Cardim De Carvalho Filho, 2001).
Resultados
Usando un análisis de sistemas y subsistemas, se puede atribuir una etapa o fase durante el ciclo de vida de un producto, en este caso el cemento portland y revisarlo durante su ciclo de vida para así analizar el impacto que generan sobre el medio ambiente, para ello Cardim de Carvalho propone analizarlo en 4 niveles e identificar en cada uno de ellos sus impactos potenciales. (Cardim De Carvalho Filho, 2001).
De esta forma podemos identificar los niveles aplicables para la producción de Cemento Portland con aditivos ( Figura 1 ) y sus impactos potenciales ( Tabla 7 ) (Cardim De Carvalho Filho, 2001).
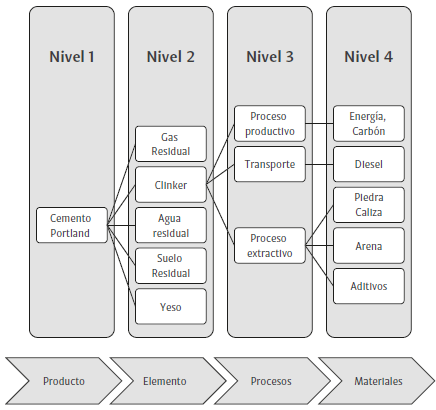
Fuente: elaborada por los autores.
Figura 1 Niveles aplicables para la elaboración del cemento Portland.
Tabla 7 Impactos ambientales producidos en la generación del cemento tipo Portland.
Producto de la producción del cemento | Impacto sobre el medio ambiente | ||
Producción | Uso y mantenimiento | Reuso | |
Materiales (Nivel 4) | • Consumo energético y de recursos naturales derivados de los procesos de transporte y extracción. • Generación de contaminación en el aire, el suelo y el agua (Transfronteriza y locales). • Generación de ruido y vibraciones. • Impacto visual. | • Impactos potenciales derivados del producto intermedio o final que lo utiliza. • Consumo energético y de recursos naturales en los procesos de mantenimiento. • Generación de residuos o sustancias tóxicas, derivados de los procesos de mantenimiento | • Impactos potenciales en el producto intermedio o final que se utiliza. |
Componente o elemento (Niveles 2 o 3) | • Consumo energético y de recursos naturales derivados de los procesos de transporte y producción. • Generación de contaminación en el aire, el suelo y el agua (Transfronteriza y locales). • Generación de ruido y vibraciones. | • Consumo energético y de recursos naturales en los procesos de mantenimiento. • Generación de residuos o sustancias tóxicas, derivados de los procesos de mantenimiento. | • Impactos potenciales en el producto intermedio o final que se utiliza. |
Cemento Portland (Nivel 1) | • Consumo energético y de recursos naturales derivados de los procesos de extractivos y productivos. • Generación de ruido y vibraciones. • Producción de residuos por excedentes de procesos de embalajes. • Generación de contaminación en el aire, el suelo y el agua (Transfronteriza y locales). Impacto visual | • Consumo energético y de recursos naturales, en los procesos de mantenimiento. • Generación de ruido y vibraciones, en función de la naturaleza de uso y su vida útil. • Generación de residuos (desechos, aguas residuales y sustancias tóxicas), derivados del mantenimiento. | • Consumo de energía en los procesos de demolición de estructuras. • Generación de ruido y vibraciones. • Emisiones de partículas al aire. • Producción de residuos por demolición descontrolada o selección para reciclado. • Consumo de energía en los procesos de transportes, selección y machaqueo (reciclado). • Impacto visual. |
Fuente: Adaptado de (Cardim De Carvalho Filho, 2001).
Los impactos ambientales de las 6 etapas (transporte, preparación de materias primas, calcinación, molienda, envasado y otros) fueron simuladas mediante el programa OpenLCA, para una unidad funcional de 1 tonelada, obteniendo las emisiones y contaminantes reflejados en la Tabla 8.
Tabla 8 Resultados totales de las categorías de impactos de un cemento tipo Portland con reemplazo de 14 % de CH y 5 % de CA.
Categoría de impacto | Resultado | Unidad de referencia |
---|---|---|
Acidificación | 1.40E+01 | mol H+ equivalente |
Agotamiento de Ozono | 6.08E-05 | kg CFC-11 equivalente |
Cambio climático | 7.84E+02 | kg CO2 equivalente |
Consumo de agua | 1.41E+03 | m3 equivalente |
Ecotoxicidad en agua dulce | 1.67E+04 | CTUe |
Eutrofización en agua dulce | 5.76E-01 | kg P equivalente |
Eutrofización en agua de mar | 2.82E+00 | kg N equivalente |
Eutrofización terrestre | 5.46E+01 | mol N equivalente |
Formación de Ozono fotoquímico | 2.20E+00 | kg COVDM equivalente |
Toxicidad en Humanos (cancerígena) | 4.43E-07 | CTUh |
Toxicidad en Humanos (no-cancerígena) | 2.24E-05 | CTUh |
Fuente: elaborada por los autores.
De igual forma, se realiza un análisis detallado de la contribución de las industrias directas o indirectas con las cuales se genera una correlación de productos y servicios para la producción de una tonelada de cemento con reemplazo de CH y CA. En la Figura 2 se puede apreciar la cantidad emanada por las industrias que más aportan CO2 dentro de la cadena productiva de este cemento. En ella se es posible observar que la industria con mayor aporte al cambio climático es la relacionada con la producción de energía en forma de combustión, la cual aporta un total de 398,10 kg de CO2 equivalente por cada tonelada de cemento con reemplazo de 14 % de CH y 5 % de CA, es decir representa cerca del 50 % de las emisiones generadas, este proceso es relacionado durante la etapa de producción en los procesos de incineración. De igual forma, la segunda industria con más aporte al cambio climático es la industria minera, la cual es responsable de la liberación 200, 10 kg de CO2 equivalente por cada tonelada de este tipo de cemento. Mientras que el resto de las emisiones de CO2 equivalente corresponden a la producción del arroz (73,38 kg de CO2 eq), la deforestación (55,02 kg de CO2 eq), la producción energética de las hidroeléctricas (32,17 kg de CO2 eq) y la producción de maíz (25,17 kg de CO2 eq), el cual es requerido como alimento de las gallinas.
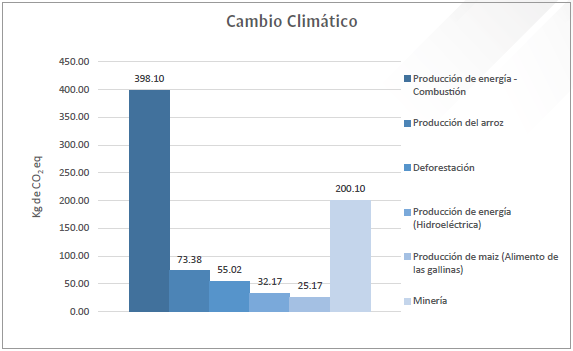
Fuente: elaborada por los autores.
Figura 2 kg de CO2 equivalente aportado al cambio climático por las industrias dentro de la cadena de producción del cemento con reemplazo de CH y CA.
Por otro lado, una de las problemáticas que genera gran impacto mundial es el uso del agua, esta problemática surge debido a la urbanización y agricultura extensiva, y se prevé que para 2030 en un escenario de cambio climático haya un déficit del 40 % del agua dulce disponible, y si a esto sumamos que el 20 % de los acuíferos del mundo están actualmente sobreexplotados (UNESCO & WWAP, 2015), genera una gran preocupación y pone en foco a la comunidad internacional frente a la cantidad de agua consumida por cada industria. De esta manera, en la Figura 3 se puede apreciar el consumo de agua requerido en la producción y mantenimiento de una tonelada de cemento con reemplazo de CH y CA. En ella se observa, que el mayor consumo de agua es requerido en la actividad minera, la cual consume 9232,60 m3 por cada tonelada de cemento con reemplazo producido, esta industria es requerida para la extracción de la materia prima base del cemento tradicional, así como el cemento con reemplazo, donde a pesar de requerir menor cantidad, sigue siendo uno de los principales elementos que componen su producción como lo son la piedra caliza y la arena extraídas por esta industria.
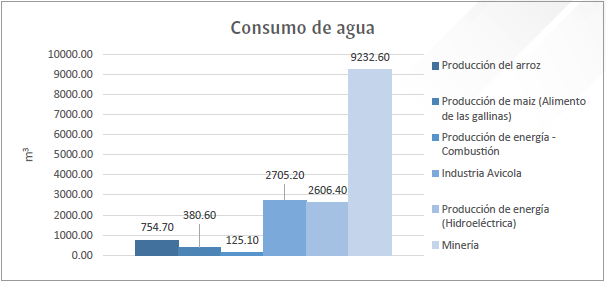
Fuente: elaborada por los autores.
Figura 3 Cantidad de agua consumida por las industrias dentro de la cadena de producción del cemento con reemplazo de CH y CA.
Siguiendo con el análisis de los impactos por industrias, es igualmente pertinente analizar el consumo de recursos. Ya que estos representan la continuidad y subsistencia del sistema productivo actual donde poseemos recursos finitos y dependiendo de la cantidad usada en cada industria implica la supervivencia de su sistema productivo actual. Además, el consumo de recursos está asociado a los impactos anteriormente estudiados y generan consecuencias tanto en las emisiones de contaminantes en el aire, suelo y agua, así como en la calidad de vida de las personas. En la Figura 4 se observa el consumo de recursos requeridos para la obtención de minerales y metales, esto reflejado en Kg de Sb (Antimonio) equivalente, estos resultados están en orden de magnitud de 10-4 - 10-5, lo que implica que este elemento no es relevante en el sistema productivo de este tipo de cemento. Sin embargo, en el caso de la Figura 5 en la cual se aprecia el consumo de recurso por combustibles fósiles en MJ, si es relevante y el mayor consumidor, como es de esperarse, es la producción energética por combustión con un requerimiento de 8123 MJ para producir una tonelada de cemento de reemplazo de CH y CA, mientras que lo sigue la industria minera con un requerimiento de 1818 MJ por tonelada de cemento producido, esto se explicaría debido a la gran cantidad de maquinaria Diesel que es usada día a día para la extracción de materia prima como la piedra caliza y la arena.
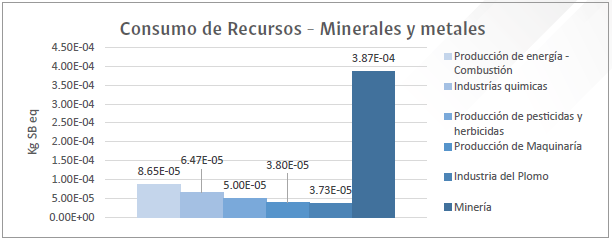
Fuente: elaborada por los autores.
Figura 4 Niveles aplicables para la elaboración del cemento Portland.
Discusión
El análisis del ciclo de vida ha sido útil para determinar los impactos ambientales asociados a todas las etapas de la producción de un cemento con reemplazo de 14 % de CH y 5 % de CA, ya que es un proceso que permite evaluar desde el inicio del huevo proveniente de las gallinas, el arroz que se cultiva en los campos y la piedra caliza extraída de las minas. Así como todo su recorrido hasta llegar a formar parte del aglutinante conocido como cemento. Mediante este análisis fue posible identificar cada una de las industrias que hacen parte fundamental del proceso y que probablemente mediante otro tipo de análisis podrían pasar desapercibidas. De esta forma, se pudo identificar que la industria minera, así como la producción de energía asociada a la combustión son los que más peso tienen en la generación de impactos. Teniendo en cuenta que por medio de esta investigación se busca evaluar y comparar las ventajas y desventajas que ofrece añadir un material de desecho como lo son la CH y la CA a la cadena de producción actual sin generar cambios en los procesos de incineración o molienda. Se puede entender entonces, que por medio de este nuevo cementante no se podrá disminuir los impactos asociados a la generación de energía por medio de combustión. Sin embargo, si se disminuye el impacto asociado a la minería extractiva al reducir la cantidad de piedra caliza y arena utilizados para la fabricación del cemento. Por otro lado, entendiendo que las investigaciones anteriores han encontrado que las CA y CH sólo requieren temperaturas de entre 500°C - 900 °C para cumplir con las propiedades de resistencia esperadas (Akhil & Kumar, 2015; Jhatial et al., 2019; Vidal et al., 2018), se encuentra un nicho de mejora en el proceso actual e implicaría una reducción significativa del impacto asociado a la generación de energía por combustión. Ya que el proceso estudiado se realizó teniendo en cuenta una incineración a una temperatura superior a los 1400 ° (Mamlouk & Zaniewski, 2009).
Por otro lado, los resultados obtenidos deben ser comparados con estudios similares. Por lo cual los valores presentados en este estudio son comparados con los obtenidos por Song et al., 2016., como se observa en la Tabla 9. Donde en dicha investigación se realiza el análisis de ciclo de vida para un cemento tradicional.
Tabla 9 Comparación de impactos de un cemento tipo Portland con reemplazo de 14 % de CH y 5 % de CA y un cemento típico tradicional.
Resultado Cemento con | Resultado de un | ||
---|---|---|---|
categoría de impacto | Unidad de referencia | reemplazo de 14 % de CH y 5 % de CA | cemento típico (Song et al., 2016) |
Acidificación | mol H+ equivalente | 1.40E+01 | 2.51E+00 |
Agotamiento de Ozono | kg CFC-11 equivalente | 6.08E-05 | 6.15E-07 |
Cambio climático | kg CO2 equivalente | 7.84E+02 | 6.78E+02 |
Consumo de agua | m3 equivalente | 1.41E+03 | 1.00E+04 |
Ecotoxicidad en agua dulce | CTUe | 1.67E+04 | 5.14E-01 |
Eutrofización en agua dulce | kg P equivalente | 5.76E-01 | 1.59E-01 |
Eutrofización en agua de mar | kg N equivalente | 2.82E+00 | 4.45E+02 |
Eutrofización terrestre | mol N equivalente | 5.46E+01 | 1.32E-02 |
Formación de Ozono fotoquímico | kg COVDM equivalente | 2.20E+00 | 1.28E-01 |
Toxicidad en Humanos | CTUh | 2.29E-05 | 8.83E-01 |
Fuente: elaborada por los autores y Song et al., 2016.
Por medio de la Tabla 9 podemos identificar que hay una disminución en los impactos asociados al consumo de agua, la toxicidad en humanos y a la eutrofización en agua dulce. Estas reducciones están asociadas principalmente a la disminución de la minería, ya que como se observa en la Figura 3, esta industria es la que más contribuye al consumo de agua. A pesar de esto se denota un aumento en los kg de Co2 equivalentes asociados al cambio climático; siendo consecuentes es un resultado que no se espera dado que una disminución de los recursos extraídos mediante minería se vería reflejado en una disminución en las emisiones de Co2. Por lo que al revisar la investigación realizada por Cardim De Carvalho Filho, 2001., se puede evidenciar en los resultados que al comparar dos métodos para realizar el ACV se identifica una disminución en la cantidad de kg de Co2 equivalentes asociados al cambio climático, como es el caso de la investigación de Song et al., 2016, donde se omiten procesos fundamentales del proceso de producción, lo que genera una reducción en las emisiones de este gas. De esta forma si se compara el valor obtenido en el presente estudio, con el de Cardim De Carvalho Filho, 2001., el cual fue de 841,71 kg de Co2 para la producción de una tonelada de cemento Portland tipo I (Cardim De Carvalho Filho, 2001), se puede apreciar una disminución significativa del impacto asociado al cambio climático, sustentando lo esperado en la presente investigación.
Así mismo, se denota un aumento en los impactos ambientales asociados a la acidificación, el agotamiento de Ozono, la Ecotoxicidad y la Eutrofización. Sin embargo, cabe resaltar que estos impactos están asociados a la producción agrícola, en este caso la producción del arroz, por lo cual, si el proceso estudiado no se llevara a cabo, estos impactos se mantendrían de igual forma e incluso aumentarían al disponer las cascarillas de arroz en un relleno sanitario. Por lo que al introducir este desecho no se estará evitando las consecuencias de su producción, pero sí se evitará el aumento de los impactos asociados a la disposición en un relleno sanitario.
Por último y como se menciona anteriormente, los procesos de producción de energía por combustión y la minería son los mayores contribuyentes al cambio climático asociados a la producción del cemento, por lo que un aumento de los porcentajes de reemplazo de CH y CA, combinado con una disminución de la temperatura requerida para su incineración pueden hacer un cambio significativo en las emisiones de gases de efecto invernadero emitidos a la atmósfera, más aún teniendo en cuenta que la producción de cemento es la segunda industria que más le aporta al planeta gases de efecto invernadero (Alfocea Roig, 2020).
Conclusiones
El uso del análisis del ciclo de vida (ACV) es un método eficaz para evaluar los impactos ambientales asociados a la producción de cemento. Así como todos los nuevos cementantes o aditivos que deseen analizar su impacto ambiental frente al proceso tradicional de elaboración. Además, permite identificar cada uno de los impactos asociados desde la materia prima, el transporte y su transformación al producto final.
De igual forma, se pudo constatar que el uso de reemplazo de 14 % de CH y 5 % de CA en un cemento Portland y su incorporación en el proceso actual, implica una disminución en todos los impactos ambientales asociados. Ya que, a pesar de se generen nuevos impactos asociados a la producción del arroz, estos impactos siempre estarán presentes debido a que es un producto alimentario de primera necesidad que genera gran cantidad de residuos al no disponer de forma adecuada su cáscara, por lo que adicionarla junto a otro desecho como las cáscaras de huevo implica una mejora encaminada a la economía circular.
Por otro lado, se debe evaluar e identificar nuevas formas para mejorar la resistencia de los cementos creados con base a porcentajes de reemplazo de material cementante con CH y CA, que permitan eliminar el uso de cemento Portland tradicional, y generar cementos a base únicamente de desechos. Esto con el fin de generar un producto que disminuya sustancialmente los impactos ambientales que contribuyen al cambio climático y que a su vez reincorporan materiales de desecho a la cadena productiva.