1. INTRODUCTION
The global population is increasing annually, and energy needs are growing daily. Fossil fuels are the most important sources of human energy worldwide. However, fossil fuel sources are not renewable and imply significant environmental risks (Zobaa & Bansal, 2011). In recent years, the ecological effects of fossil fuels have become increasingly evident. Global warming has led to the melting of polar ice caps, endangering the lives of all organisms. Natural fires and storms are sources of significant hazard.
Therefore, alternative clean energy sources for fossil fuels have received considerable attention recently. Solar, wind, water, fuel cell, geothermal, and biomass energy are renewable sources (Kurchania, 2012). Choosing a clean energy production method depends on various factors, including geographical and biological conditions and operating costs. In addition, energy conversion processes must be free of environmental hazards, and their adverse effects, such as extreme heat production and environmental pollutants, must be avoided. (Nordin, 2010). Likewise, energy conversion processes must be free of environmental hazards, and their adverse effects, such as extreme heat production and environmental pollutants, must be avoided. Among the clean energy production methods, wind and water have the lowest cost, whereas the highest cost is solar power Geothermal energy is one of the best solutions for producing renewable energy, given its various benefits. Unlike other renewable energy sources constrained by certain seasons, timing, and environmental factors, geothermal energy can be used continuously. Further, the cost of electricity in geothermal power plants is competitive with that of other standard (fossil) power plants and even cheaper than other new energy types. Therefore, geothermal resources are valuablebecause of their availability, simple technology for creating power plants, possibility of uninterrupted operation, and long-term use (Karki, 2009).
The ability of N2O, CO2, and H2O EGS to extract heat has been compared by Liu et al. (2022). A two-dimensional thermo-hydraulic-mechanical (THM) coupled EGS model with discrete fractures was created. The effects of the injection-production parameters on the heat-extraction outcomes of the EGS employing various working fluids were also examined. The results demonstrate that, under the same conditions, N2O-EGS and CO2-EGS performed almost exactly during heat extraction. Sahana et al. (2021) suggested employing a supercritical CO2 power cycle to recover heat from the HWCS when hot water is delivered from an oilfield at a temperature close to 140 °C. The output of the supercritical CO2 power cycle drives the compressor of the ejector-expansion CO2 refrigeration cycle. Using some CO2 cycles to reject heat, the humidification-dehumidification (HDHn) unit may produce fresh water. In a study, Wang et al. (2019) used supercritical CO2 (sCO2) to simulate geothermal heat mining. The requirements for choosing the working fluid for organic Rankine cycles (ORCs) that use sCO2 from a geothermal reservoir are then given for subcritical, superheated, and supercritical ORCs. In this study, a practical fluid classification method for ORC was proposed. Models were used by Jiang et al. (2017) to predict efficiencies of standalone and hybrid systems. It was found that the hybrid system has an efficiency that is on par with or even higher than the combined efficiency of the two individual CO2-EGS and CO2-solar thermal systems compared to standalone CO2-EGS and CO2-solar thermal systems.
According to Liu et al. (2020) research, the compression techniques used in supercritical CO2 (S-CO2) and transcritical CO2 (T-CO2) power cycles differ, and their implications for the equipment's and power cycles' thermodynamic performance are explored. According to the data, there was a significant increase in the thermal efficiency and net output power close to the critical temperature, while the overall compressor/pump inlet temperature decreased. A recompression supercritical carbon dioxide Brayton cycle, coupled with a solar power tower, was proposed and studied by Cao et al. (2022). Two energy-storage stages were used to increase the stability of the solar subsystem for continuous daily operation. In addition, a solid oxide electrolyzer was included in the plan. Liu et al. (2021) used conventional and advanced energy evaluations to assess the exergetic performance within the transcritical CO2 ejector refrigeration system integrated with a thermoelectric subcooler (EJE + TES). The findings show that 89.44% of the total energy destruction is endogenous, meaning that there is no close relationship between the system's constituent parts.
This study compared two operating modes of a single flash geothermal cycle-"Without Economizer" and "With Economizer"- powered by a trans-critical carbon dioxide cycle. Both systems were modeled in the EES software after being designed based on thermodynamic equations and thermodynamics' first and second laws. Adding an economizer to the system and studying its effects on output parameters (such as energy efficiency, energy efficiency, and net power output) and the system's performance are the primary novelties of this study. Furthermore, a sensitivity analysis was performed to examine the impact of modifications to the system's critical parameters on both operating modes' energy efficiency, energy efficiency, and net power output. The main aims of this study were:
Simulating a single flash geothermal power plant in both "Without Economizer" and "With Economizer" operating modes ,using a transcritical CO2 Cycle.
An analysis comparing the two operating modes, "With Economizer" and "Without Economizer."
Variations in net power output, energy efficiency, and energy efficiency concerning system critical parameters.
A sensitivity analysis of the economic parameters and an economic analysis of the "with economizer" and "without economizer" systems.
Typically, thermodynamic equations and primary data are used to model suggested systems in an EES software environment, and the output results are compared. The output parameters (energy efficiency, energy efficiency, net power output, total cost rate, and production cost rate) of the systems are shown and discussed in the form of comparative diagrams for both working modes with the changes in separator pressure, CO2 turbine inlet pressure, and CO2 condenser temperature.
2 PROPOSED SYSTEM DESCRIPTION
Suppose that geothermal power plants are compared to other new energy power plants. Geothermal power plants are essential worldwide because of their high availability factor (85% of the time per year), and these power plants can be used as the base load of the network (Gürbüz et al., 2022). Beneath the Earth's surface is a layer of hot and molten rock called magma, which continuously produces heat from radioactive substances such as uranium and potassium. This heat can have 50,000 times more energy than oil and gas sources. Areas where the earth's temperature is high due to volcanoes, or the earth's crust is thin, are considered for this industry. The edge of the Pacific Ocean and the ring of volcanoes were introduced as the best options. The vibration of earthquakes, magma, hot rocks, and Earth's crust allows water to move upward and create hot water springs (Bajogul et al., 2021).
The concept of EGS (Enhanced Geothermal Systems) originated from the old idea of HDR (Hot and Dry Rocks) at the Los Alamos National Laboratory in the United States. Hot and dry rocks in some places deep on Earth are called dry sources because of the lack of hot water or steam (Mahmoudan et al., 2022). It is evident that the use of dry resources is possible, and the significant development of technology in the last few decades has enabled human access to the problematic part of energy hidden in Earth, called improved geothermal energy. Enhanced geothermal systems (EGS) contain vast reserves of renewable energy. The main goal of related studies is to create flow paths between underground rocks to facilitate heat transfer, or increase permeability for circulating large volumes of water (or other working fluids), and injecting water into hot rocks deep in the ground to exploit this potential (Yargholi et al., 2020). This is the heat of the hot stones. Water can be injected to the desired depth so that, after heating, it is directed to the Earth's surface in the form of steam or hot water (Hoseinzadeh et al., 2020).
The single-flash geothermal cycle driven by the trans-critical carbon dioxide cycle is shown in Figures 1(a) and 1(b) in "Without Economizer" and "With Economizer" working modes. The Engineering Equation Solver (EES) software simulates the system. In the simulation approach, each system component was used to control-volume engineering, and the first and second laws of thermodynamics were applied.
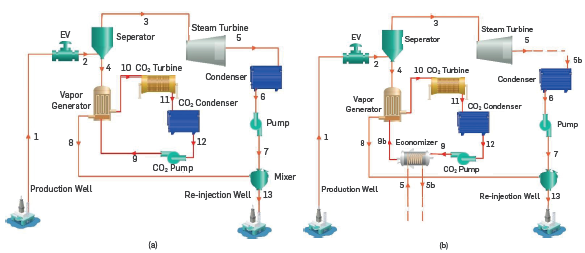
Figure 1 Schematic of the proposed single flash geothermal cycle powered by a trans-critical CO2 (a) Without Economizer (b) With
During the decompression process, in which the pressure is reduced while maintaining a constant enthalpy, the geo-fluid that enters the system is transformed into a two-phase fluid, as illustrated in Figure 1(a). The steam turbine was powered by the saturated vapor component of the two-phase fluid that moved into the separator. The vapor generator (VG), which increases the temperature of the carbon dioxide gas before the heat exchanger outlet fluid is routed to the ground, receives the saturated liquid component of the separator. It is delivered to the gas turbine at an appropriate pressure and temperature, producing more power for the entire system.
Figure 1(b) shows the installation of an economizer between the CO2 pump and VG to enhance system efficiency. The output stream of the steam turbine (point 5) enters the economizer and warms the CO2 pump's output stream before it reaches the condenser (point 9). Determining the congestion point in a trans-critical cycle is difficult because the slope of the temperature changes when carbon dioxide gas heats up within heat exchangers, such as an evaporator. The temperature difference between the beginning and end was considered constant for ease of solution.
There are two significant differences between EES software and other software that use numerical solution methods:
1) The EES software can automatically identify equations that are to be solved together, and this feature allows the EES software to solve the equations in the shortest possible time.
2) EES software has many thermodynamic and internal mathematical functions, which are helpful in engineering calculations in thermodynamics, fluid mechanics, and heat transfer. For example, property tables for different materials are available in EES software, and it is possible to obtain the desired property having two independent properties for materials. Moreover, property tables for different materials are available in EES software, and it is thus possible to obtain the desired property by having two independent properties for materials. Furthermore, the EES software can read programs written in Pascal, C, and Fortran programming languages. One of the most salient features of EES software is its parametric study ability, provided by its parametric table. By entering the values of the independent variables in this table, the corresponding values of the dependent variables were calculated, and the relationships between the different parameters in this table can be shown as graphs.
3 GOVERNING EQUATIONS
The first law of thermodynamics is typically viewed as a different interpretation of energy conservation law. The energy was neither generated nor destroyed. Instead, according to the principle of conservation, it transforms from one form to another. The first rule of nature is the second law of thermodynamics, so this law is absolutely one of the most valuable discoveries made by man. This law is difficult to understand for most researchers and engineers. This is because it involves numerous complex concepts such as enthalpy, entropy, and Gibbs free energy. The first definition of the second law of thermodynamics is Clausius's law. According to this definition, it is impossible to build a cycle engine or a cycle whose sole effect is to continuously transfer heat from a source with a higher temperature to a head with a lower temperature. In simple terms, building a refrigerator that can receive energy from a lower-temperature source (cold source) and transfer it to a higher-temperature source (hot source) is only possible by doing work. The second definition of the second law of thermodynamics is the Kelvin-Planck definition. According to this definition, building a cycle heat engine that can operate equal to the heat absorbed from the source is not possible. The efficiency of such an engine is 100%, a dream that human kind has had for years, which is an unattainable goal. In other words, the heat engine cannot convert all the energy obtained from the heat source in one cycle into work, but part of the energy received from the hot start is given to the cold source as wasted energy.
According to equations (1) and (2), and ignoring the kinetic and potential energies, the system is written while considering the control volume, mass, and energy balances for each component of the system (2) (Melzi et al., 2021; Pambudi et al., 2021; Parikhani et al., 2021; Saengsikhiao et al., 2021; Yazarlou & Saghafi, 2021):
where ṁ ¡ is the input flow rate and ṁ o is the output flow rate. Also, h ¡ is the enthalpy of the input flow, and h o is the enthalpy of the output flow. W is the work and Q is the exchanged heat. Equations (3) and (4) yield each turbine's isentropic efficiency and net power production, respectively.
The isentropic efficiency and net power of each pump are expressed as
Equations (7), (8), and (9) represent the net power of the system, as well as the energy efficiency and energy efficiency of the entire system (Chen et al., 2021; Mohtaram et al., 2021; Wang et al., 2015):
In the current investigation, the following hypotheses were considered (Aali et al., 2017; El Haj Assad et al., 2021; Sun et al., 2020):
All cycle parts function in steady-state situations (as control volume).
The changes in the kinetic energy and potential in all components are insignificant, and the pressure drop and heat loss in the pipelines can be disregarded.
The isotropic efficiency of the pumps is 0.75, whereas that of the turbines is 0.8.
The ambient temperature and pressure used for analysis were 25 °C and 0.1 MPa, respectively.
The increase in energy demand in the 21st century comes along with problems such as environmental pollution, lack of natural resources, limited space, and suitable places to construct fossil fuel power plants. However, the growth of technology worldwide has increased the demand for energy, especially electrical energy. From this perspective, it is essential to determine alternative clean energies, irreversibility factors in energy-consuming systems, and optimal energy consumption using thermoeconomic analysis. In thermo-economic analysis, thermodynamics is combined with economic concepts to improve the design of systems. The most efficient system can be identified by considering economic issues while minimizing the price and operating time of the system. The cost-rate balance for the entire system can be stated as follows in the economic analysis (Mosaffa et al., 2017):
Where Ċ total (=c product Ẇ net ) and Ċ fuel (=c G Ėx 1 ) represent the respective total (or product) and fuel-cost rates. The following are estimates of the total running, maintenance, and capital expenditure cost rates for each system component (Bejan et al., 1995):
Zk is the investment cost of each component, Ø maintenance coefficient, N is the number of annual operating hours, and CRF is the return on investment coefficient. CRF can be calculated according to the following expression (Bejan et al., 1995):
Therefore, "¡" is the interest rate and " n" is the useful life of the system. The investment cost functions of each system component are listed in Table 1.
Calculating certain factors in economic research, such as the total cost, return on investment, and cost of producing an energy unit, might help clarify the situation.
That Ċ tot tot shows the total cost rate of the system and p roduct is product cost. Table 2 presents the essential data required for the system simulation in the software environment. One of the main components of any application is the data that is used. Familiarity with data types in programming helps to use them correctly. This will improve the performance and speed of programming.
4 RESULTS AND DISCUSSION
In this section, the performance of the proposed systems is assessed and analyzed, and the findings of the energy, energy, and economic analyses are presented in tables and figures. The nput parameter values are listed in Table 1 to determine how the different parameters affect the system's performance. Temperature, pressure, mass flow rate, enthalpy, and entropy are the four thermodynamic parameters for the "Without Economizer" system in Table 3 and the "With Economizer" system in Table 4.
Table 3 Thermodynamic properties of the different points of the system in "Without Economizer" working mode
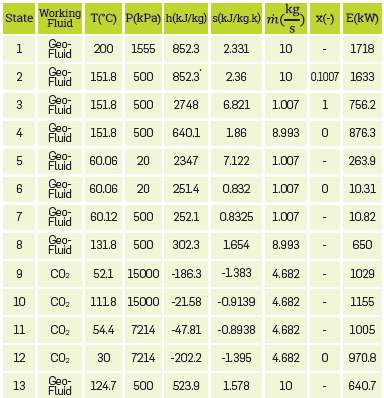
Table 4 Thermodynamic properties of the different points of the system in “With Economizer” working mode.
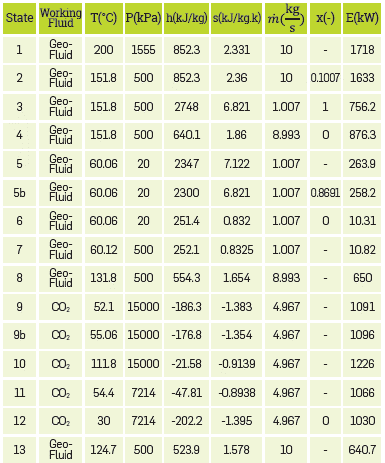
Table 5 shows the output results from the systems simulation in two "Without Economizer" and "With Economizer" working modes. One of the crucial features in Table 5 is the increase of the net power output from 451.3 kW to 454 kW, which indicates a 0.598% increase in the "With Economizer" system. Regarding energy efficiency this value is 6.036% for the "Without Economizer" system, and reaches 6.075% in the "With Economizer" system, that is, a 0.646% improvement from the perspective of the first law of thermodynamics. Regarding energy efficiency, the value of this efficiency for the "without economizer" system was 26.26%. The "with economizer" system reached 26.43%, representing an improvement of 0.647% from the second Law of thermodynamics or energy standpoint. From an economic perspective, the total cost rate of the primary system is 0.225 M$/ Year. With the addition of the economizer, this value reaches 0.2294 M$/Year, representing an increase of 1.955% in this parameter. As for product cost rate, this parameter is 15.82$/G J for the basic system, and with the addition of the economizer, this value reaches 16.02$/ GJ, that is, an increase of 1.264%.
Table 5 Output results from the simulation of systems in two "Without Economizer" and "With Economizer" working modes.
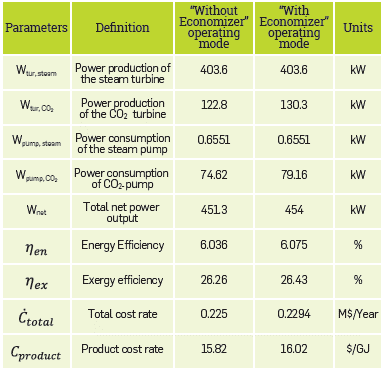
In sum, the results suggest that adding an economizer to the proposed single-flash geothermal system powered by a trans-critical carbon dioxide cycle leads to an improvement of approximately 0.60.65% in the studied system's energy and energy output parameters. Figures 2(a), (b), and (c) show the changes in energy efficiency, energy efficiency, and total output work of the system equipped with an economizer concerning the changes in separator pressure for inlet temperatures (Tl) of 190, 200, and 210°C.
First, it should be noted that the higher the system inlet temperature, the better the system performance. This is illustrated in Figure 2, By increasing the separator pressure from 150kPa to 650kPa, the system's energy efficiency first increased, reached a maximum point, and then decreased. From the energy efficiency perspective, this maximum point is the most suitable separator temperature for an ideal system performance. This ideal pressure equals 270.7kPa, 305.2kPa and 339.4kPa for temperatures of 190°C, 200°C and 210°C, respectively. As for the energy efficiency, with the increase in separator pressure from 150kPa to 650kPa, the energy energy efficiency first increased, reached a maximum point, and then decreased. Relative to energy efficiency, this maximum point is the most suitable separator temperature for an ideal system performance. This ideal sharp pressure equals 270.7kPa, 305.2kPa and 339.4kPa for temperatures of 190°C, 200°C and 210°C, respectively. From the total output work perspective, the figures' behavior is similar to the energy and energy efficiency.
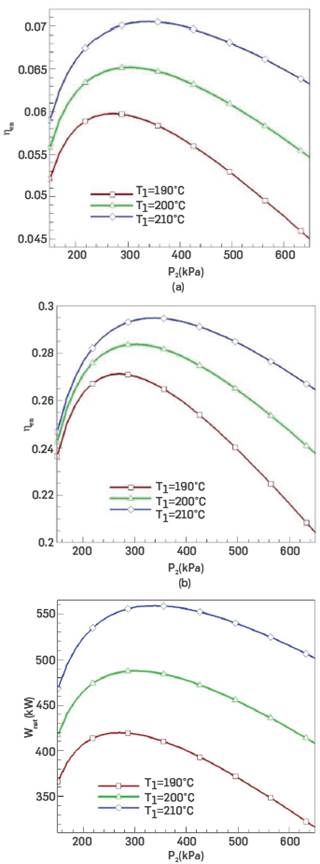
Figure 2 The effect of separator pressure changes on (a) energy efficiency, (b) energy efficiency and (c) net power output of the system equipped with an economizer at inlet temperatures of 190°C, 200°C and 210°C.
The Limitations of the current study are:
Geothermal Resource Availability: One of the limitations of implementing a trans-critical CO2 cycle powered by a singleflash geothermal cycle is the availability of suitable geothermal resources. The success of this system relies heavily on the availability and quality of geothermal reservoirs, which can support robust and efficient operations.
Technological Challenges: Various technological challenges may be associated with implementing a trans-critical CO2 cycle in geothermal power plants. These challenges include designing and optimizing heat exchangers, selecting appropriate working fluids, and developing efficient control strategies for optimal performance. Overcoming these challenges requires extensive research and development efforts.
System Efficiency: While a trans-critical CO2 cycle powered by a single-flash geothermal cycle has the potential to be highly efficient, there may be limitations to achieving optimal performance. Operational and design factors such as temperature and pressure limitations may affect cycle efficiency. Finding ways to enhance the system efficiency and maximize the power output would be an area of interest for future research.
Economic Viability: Another limitation is the feasibility of implementing a trans-critical CO2 cycle with an economizer in a geothermal power plant. Assessing the cost-effectiveness of this system, including the capital investment required, maintenance costs, and potential revenue generation, is crucial for determining its viability and long-term sustainability.
The future research directions of this study include :
Optimization of Heat Exchangers: Future research could focus on optimizing heat exchanger designs to enhance the heat transfer efficiency between the geothermal and CO2 working fluids. This could involve exploring advanced heat-transfer enhancement techniques, such as enhanced surfaces or novel heat-exchanger configurations, to maximize the heat-transfer rate and overall system performance.
Development of Advanced Control Strategies: Efficient control strategies are essential for successfully operating a trans-critical CO2 cycle powered by a single-flash geothermal cycle. Future research could explore advanced control algorithms, such as model predictive control or artificial intelligence-based approaches, to optimize system operation, maximize power output, and ensure safe and stable operation under varying geothermal conditions.
Environmental Impact Assessment: Evaluating the environmental impact of implementing this technology is crucial. Future research could focus on conducting comprehensive life cycle assessments to analyze the environmental footprint of a trans-critical CO2 cycle with an economizer compared to conventional geothermal power plants or other renewable energy sources. This assessment would help identify the technology's potential environmental benefits and limitations.
Techno-economic Analysis: Further research should be conducted to evaluate the techno-economic feasibility of implementing a trans-critical CO2 cycle in geothermal power plants. This includes assessing the overall cost-effectiveness, calculating the leveled cost of electricity, and conducting economic sensitivity analyses to identify the key factors influencing the system's economic viability.
System Integration and Flexibility: Investigating the integration of a trans-critical CO2 cycle with other energy systems and grid integration is an important area for future research. This would involve studying the potential for hybridization with other renewable energy sources, such as solar or wind, and exploring the system's flexibility to adapt to the changing grid demands and conditions.
By addressing these limitations and focusing on future research directions, implementing a trans-critical CO2 cycle powered by a single flash geothermal cycle equipped with an economizer could be further enhanced, thus improving efficiency, economic viability, and environmental sustainability.
CONCLUSIONS
A trans-critical CO2 cycle powered by a single-flash geothermal cycle with an economizer is a promising technology for efficiently harnessing geothermal energy. This system combines geothermal energy extraction using a flash cycle with carbon dioxide (CO2) as the working fluid. In a single-flash geothermal cycle, high-pressure geothermal fluid is fed into a flash tank, which rapidly decreases pressure, causing a part of the fluid to vaporize and generate steam. This steam was then used to drive the turbine and generate electricity. The remaining liquid is reinjected back into the geothermal reservoir. By integrating a trans-critical CO2 cycle into this setup, the unused heat from a single flash cycle can be further utilized. An economizer, an additional heat exchanger that extracts heat from the geothermal fluid after it exits the flash tank, is part of this setup. This additional heat transfer maximizes energy extraction from the geothermal fluid before reinjection.
In the trans-critical CO2 cycle, CO2 acts as the working fluid, which has several advantages over traditional fluids such as steam. CO2 is environment-friendly, has a lower critical temperature, has better thermodynamic properties, and allows for a more compact system design. The trans-critical CO2 cycle operates above its critical point, where the CO2 fluid undergoes a phase change from gas to liquid without condensation. This cycle utilizes the heat extracted from the geothermal fluid to raise the temperature and pressure of CO2, enabling energy conversion through expansion in a turbine. The economizer in this system plays a crucial role in transferring heat from the geothermal fluid to the CO2 working fluid. This allows CO2 to reach higher operating temperatures in the turbine, improving energy conversion efficiency.
The research highlights a significant finding: the net power output increased from 451.3 kW to 454 kW, indicating a 0.598% increase in the "With Economizer" system. According to the first rule of thermodynamics, there is a 0.646% gain in energy efficiency between the "Without Economizer" system's 6.036% and the "With Economizer" system's 6.075%. Concerning energy efficiency, the system "without an economizer had a value of 26.26%. According to the second law of thermodynamics, or energy, the "with economizer" system achieves 26.43%, which is an improvement of 0.647%.
From an economic standpoint, the baseline system's total cost rate is 0.225 M$/Year; however, the economizer installation raises this value to 0.2294 M$/Year, or a 1.955% increase in this parameter. When considering the product cost rate, the value of this parameter is 15.82$/GJ for the base system, and it increases by 1.264% to 16.02$/GJ adding the economizer.
Overall, a trans-critical CO2 cycle powered by a single-flash geothermal cycle with an economizer translates into several benefits. It maximizes the utilization of geothermal energy, improves energy conversion efficiency, and reduces the environmental impact compared to conventional power generation methods. Furthermore, this technology has the potential for widespread deployment in geothermal-rich areas, thus contributing to clean and sustainable energy production.